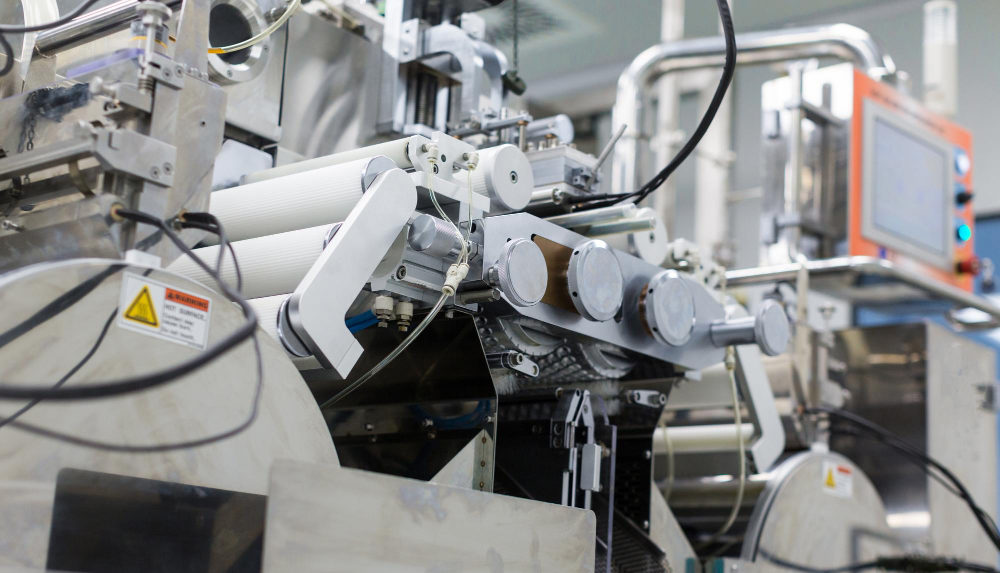
Standardizzare i Processi di Assemblaggio con Lean Six Sigma
La competitività delle multinazionali nel settore manifatturiero è strettamente legata alla capacità di ottimizzare i processi produttivi, garantendo un’elevata qualità del prodotto finale. Questo articolo esplora l’implementazione della metodologia Lean Six Sigma in una multinazionale leader nel settore della progettazione e produzione di macchinari per la trasformazione ed il confezionamento della carta tissue, che ha affrontato una sfida complessa di standardizzare i processi di assemblaggio. Grazie al supporto di Crossnova, l’azienda ha potuto migliorare le performance operative, ridurre le inefficienze e ottimizzare l’intero processo produttivo.
La sfida: eliminare i Tempi NVA e standardizzare i processi di assemblaggio
La multinazionale si trovava a fronteggiare difficoltà significative nel processo di assemblaggio, che influivano negativamente sulla rapidità di produzione e sulla qualità del prodotto finale. Da un’analisi preliminare è emersa l’assenza di standardizzazione e di documentazione tecnica adeguata, soprattutto in merito al cablaggio degli impianti elettrici e fluidici. Questa mancanza generava variabilità elevata e difficoltà operative che si riflettevano sui risultati finali.
Le principali sfide individuate erano:
- Mancanza di un processo di cablaggio standardizzato: L’assenza di una procedura univoca per il cablaggio portava a discrepanze operative tra gli operatori, generando ritardi e incertezze. Ogni macchina veniva assemblata in base a interpretazioni soggettive o metodi non uniformi. Ciò non garantiva omogeneità nei risultati e creava confusione, generando inefficienza e rischi di errori.
- Tempi non a valore aggiunto (NVA): L’operazione di foratura e assemblaggio richiedeva tempi eccessivamente lunghi, dovuti alla mancanza di disegni tecnici chiari e dettagliati. Gli operatori si trovavano spesso a improvvisare o a dover verificare più volte le operazioni, prolungando tempi che non apportavano valore al prodotto. L’assenza di documentazione causava anche interruzioni non pianificate, impedendo un flusso produttivo continuo e aumentando i costi operativi.
- Ritardi e difetti di qualità: La mancanza di una documentazione aggiornata e completa non solo rallentava i tempi di consegna, ma comprometteva la qualità finale del prodotto. Errori o incongruenze nel cablaggio e nell’assemblaggio si traducevano in difetti che richiedevano rilavorazioni o correzioni.
L’obiettivo del progetto era dunque quello di eliminare le attività non a valore aggiunto, standardizzare il processo di assemblaggio e garantire una maggiore coerenza operativa attraverso la metodologia Lean Six Sigma.
Analisi del processo: definizione e caratterizzazione del problema
Per affrontare questa situazione, Crossnova ha intrapreso un’analisi approfondita del processo utilizzando diversi strumenti di Lean Six Sigma. E’ stata fatta una misurazione accurata dei tempi non a valore aggiunto (NVA) e un’identificazione puntuale delle inefficienze tramite tecniche avanzate di Data Analysis. Questo approccio è stato progettato per aumentare la comprensione delle aree del processo che presentano sprechi, consentendo interventi mirati e strutturati per migliorare l’efficienza complessiva.
SIPOC e Mappatura del Processo
Il primo passo è stato la creazione di un diagramma SIPOC (Supplier, Input, Process, Output, Customer), che ha permesso di mappare l’intero processo di assemblaggio e individuare i principali punti critici. Questo strumento ha aiutato a ottenere una visione chiara delle attività coinvolte, evidenziando le aree dove si accumulavano le inefficienze.
Identificazione dei Tempi Non a Valore Aggiunto (NVA)
Succesivamente il Team Crossnova ha effettuato un’analisi approfondita sui tempi non a valore aggiunto (NVA) all’interno del processo produttivo. E’ stato adottato il metodo del Time and Motion Study, una tecnica consolidata per mappare e misurare i tempi di ciascuna operazione. E’ emerso che le operazioni di foratura e taglio, considerate essenziali ma non dirette alla creazione di valore, rappresentavano ben il 55% del tempo complessivo dedicato alle attività NVA. Queste attività, pur necessarie, non erano ottimizzate e presentavano margini significativi di miglioramento. Tali percentuali indicano una rilevante opportunità di riduzione dei tempi improduttivi, che potrebbe comportare notevoli benefici in termini di efficienza complessiva.
Per verificare e validare i dati raccolti, Crossnova ha utilizzato strumenti statistici e grafici, in particolare scatter plot e box plot. Questi grafici hanno permesso di visualizzare la dispersione dei tempi e la loro distribuzione, evidenziando una marcata variabilità nei tempi di lavorazione, soprattutto durante le prime fasi di assemblaggio.
In particolare, lo Scatter Plot ha mostrato come i tempi di foratura e taglio oscillassero in modo considerevole, evidenziando pattern di variabilità legati a diversi fattori, come l’abilità dell’operatore, la specificità del componente e le condizioni degli strumenti utilizzati. I punti dati, distribuiti in modo eterogeneo, suggerivano la necessità di standardizzare ulteriormente il processo per ridurre tali fluttuazioni.
Il Box Plot, invece, è risultato utile per comprendere la distribuzione e l’ampiezza dei tempi di lavorazione e ha evidenziato come molte operazioni si collocassero fuori dai valori tipici, con numerosi outliers rappresentativi di eccessi temporali significativi. La variabilità tra il primo e il terzo quartile risultava ampia, indicando che le operazioni presentavano tempi non omogenei che creavano colli di bottiglia nelle fasi iniziali del processo di assemblaggio.
Analisi delle cause: Diagramma di Ishikawa e evidenze statistiche
Per identificare le cause principali dei ritardi e delle difettosità, Crossnova ha utilizzato il diagramma di Ishikawa (noto anche come Diagramma a Lisca di Pesce). Questo strumento è stato fondamentale per strutturare un’analisi completa delle possibili cause di inefficienza, suddividendole in categorie specifiche: macchinari, manodopera, metodi e materiali. Attraverso questo strumento, il team ha potuto visualizzare e analizzare sistematicamente le cause principali, creando le basi per una successiva analisi quantitativa dei dati e l’esecuzione di test delle ipotesi per validare i risultati e individuare le correlazioni tra i fattori.
Cause identificate
- Mancanza di Strumenti di Pianificazione: La pianificazione del lavoro non era supportata da strumenti efficaci, causando ritardi e una gestione non ottimale delle risorse. L’analisi ha mostrato che circa il 25% dei ritardi era legato a una pianificazione inefficace. I test delle ipotesi condotti hanno confermato una correlazione significativa tra la mancanza di pianificazione e l’aumento dei tempi di produzione, con un incremento medio dei tempi di lavorazione del 15-20% rispetto alle lavorazioni pianificate.
- Assenza di Standardizzazione: Non esisteva una documentazione tecnica standard per guidare il cablaggio degli impianti elettrici e fluidici, obbligando gli operatori a prendere decisioni improvvisate durante l’assemblaggio.L’assenza di standardizzazione ha inciso per il 40% sui difetti di qualità riscontrati nel prodotto finale. Le analisi statistiche, tra cui test delle ipotesi sulle percentuali di difettosità, hanno dimostrato che i lotti prodotti senza linee guida precise presentavano un tasso di errore del 30% più elevato rispetto ai lotti per cui erano disponibili istruzioni dettagliate.
- Problemi di Coordinamento e Formazione: La mancanza di una figura di controllo dedicata e di programmi di formazione specifici per i fornitori esterni contribuiva a rallentare il processo e a incrementare i difetti di qualità.Si è osservato che il 35% dei difetti di qualità derivava direttamente da interventi non coordinati o da errori dei fornitori esterni. L’analisi dei dati ha evidenziato una riduzione dei difetti fino al 50% nei casi in cui il personale era stato coinvolto in sessioni di formazione dedicate e con una supervisione specifica.
Implementazione delle soluzioni Lean Six Sigma
Dopo aver completato l’analisi del processo e identificato le cause delle inefficienze, il team di Crossnova ha generato ed implementato una serie di soluzioni mirate a migliorare la qualità e la puntualità delle consegne, riducendo i tempi di assemblaggio e le attività NVA.
1. Creazione di una Documentazione Tecnica Standard (DBM)
È stato sviluppato un Documento di Cablaggio Standard (DBM), che include disegni dettagliati, foto e schemi tecnici per ogni tipologia di macchina. Questo documento ha permesso di eliminare la necessità di decisioni improvvisate da parte degli operatori, migliorando la coerenza operativa e riducendo la probabilità di errori.
2. Introduzione di foratura e taglio pre-assemblati
Grazie alla collaborazione con i fornitori, è stato implementato un processo di foratura e taglio pre-assemblati, che ha permesso di inviare i pezzi già pronti per l’assemblaggio finale. Questo ha ridotto drasticamente i tempi necessari per queste operazioni, consentendo agli operatori di concentrarsi sulle attività a valore aggiunto.
3. Utilizzo di sistemi digitali per la gestione documentale
Per migliorare la comunicazione e l’accesso alle informazioni, sono stati introdotti totem digitali all’interno della fabbrica, che consentivano agli operatori di visualizzare rapidamente la documentazione necessaria. Questo ha eliminato i tempi di ricerca e migliorato l’accessibilità alle informazioni.
Risultati misurabili ottenuti con Lean Six Sigma
L’implementazione delle soluzioni Lean Six Sigma ha portato a una serie di miglioramenti misurabili che hanno avuto un impatto significativo sull’efficienza operativa e sulla qualità del prodotto finale.
Riduzione dei Tempi NVA del 60%
L’adozione di forature pre-assemblate e l’introduzione di una documentazione standardizzata ha portato a una riduzione del 60% dei tempi non a valore. Questo è stato determinante per eliminare molte inefficienze, che rappresentavano un collo di bottiglia nel flusso produttivo. La documentazione standardizzata ha fornito linee guida chiare e dettagliate per gli operatori, aumentando la precisione delle operazioni.
Inoltre, il processo di foratura pre-assemblato ha snellito le fasi di montaggio, consentendo agli operatori di concentrarsi su attività più strategiche. L’effetto combinato di questi interventi ha portato a un aumento dell’efficienza operativa, con tempi di assemblaggio inferiori e una qualità del prodotto finale significativamente migliorata. La standardizzazione ha inoltre facilitato il trasferimento di competenze tra operatori, riducendo la dipendenza dall’esperienza individuale.
Miglioramento della puntualità delle consegne
Grazie ad una pianificazione dinamica e all’ottimizzazione delle risorse, la puntualità delle consegne ha registrato un un incremento del 20%. Questo risultato è stato possibile attraverso l’adozione di sistemi di pianificazione flessibili. Questi hanno permesso di adattare rapidamente le attività produttive in base alle variazioni della domanda e alla disponibilità delle risorse. L’ottimizzazione delle risorse ha reso più efficiente l’assegnazione di macchinari e manodopera, garantendo una distribuzione più bilanciata del carico di lavoro.
Riduzione delle difettosità del 20%
La standardizzazione del processo ha contribuito a una riduzione delle difettosità del 20%, migliorando la qualità complessiva del prodotto e riducendo la necessità di rilavorazioni. Grazie a istruzioni operative univoche e a procedure uniformi, gli operatori sono stati in grado di svolgere le attività seguendo linee guida precise. Tutto ciò ha consentito di ridurre il rischio di errori causati dall’improvvisazione o dalle differenze nei metodi di lavoro.
Monitoraggio e controllo continuo dei processi
Per garantire che i miglioramenti fossero sostenibili nel tempo, l’Azienda, con la guida del Team Crossnova, ha introdotto un sistema di monitoraggio continuo basato su KPI chiave, come la percentuale di difettosità e i tempi di assemblaggio.
In conclusione, questo progetto dimostra come l’applicazione di Lean Six Sigma porti a significativi miglioramenti operativi e a una riduzione degli sprechi nei processi produttivi. Grazie all’approccio strutturato e metodologico di Crossnova, la multinazionale ha ottenuto risultati tangibili, migliorando la qualità del prodotto, riducendo i costi operativi e aumentando l’efficienza.
Se anche la tua azienda desidera ottimizzare i processi produttivi e ridurre gli sprechi, Contattaci Subito per saperne di più!