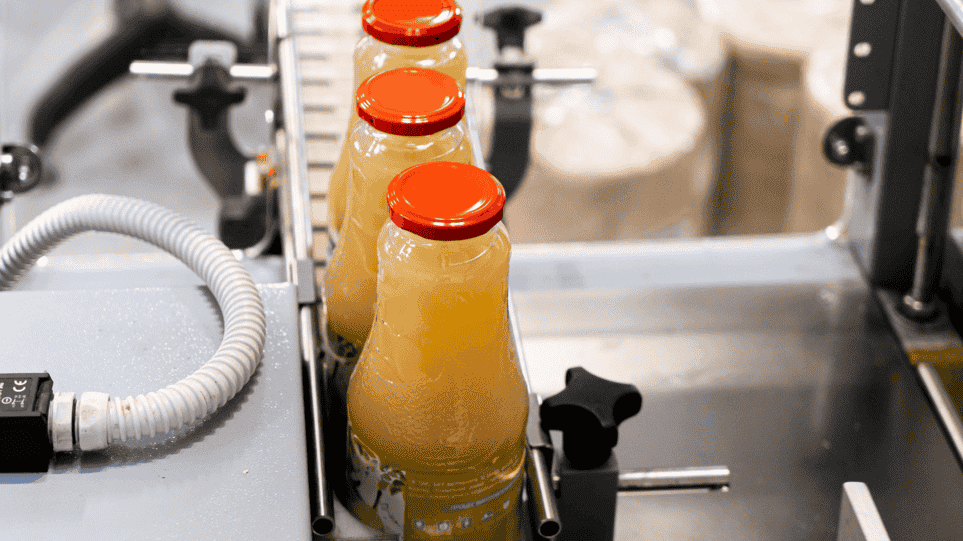
Velocità e efficienza: Come ridurre drasticamente i tempi di set-up con il metodo SMED
In questo articolo, illustreremo come ridurre drasticamente i tempi di set-up con il metodo SMED. Nel settore manifatturiero, ottimizzare i tempi di set-up rappresenta un fattore chiave per incrementare la produttività, migliorare l’efficienza operativa e abbattere i costi. Ridurre i tempi di inattività durante i cambi formato permette alle aziende di rispondere in modo più rapido e flessibile alle richieste di mercato, garantendo una produzione continua e meno sprechi.
In questo articolo, analizzeremo il caso di una vetreria che ha implementato la metodologia SMED (Single-Minute Exchange of Die) con risultati sorprendenti. Questo approccio, che si basa sulla separazione delle attività interne ed esterne al processo di set-up, ha consentito di dimezzare i tempi necessari per i cambi formato, migliorando la gestione delle risorse e riducendo i colli di bottiglia.
Grazie a tecniche strutturate e a un’attenta analisi del processo, l’azienda ha ottimizzato l’uso dei macchinari, ottenendo non solo un aumento dell’efficienza produttiva, ma anche una maggiore competitività sul mercato. Attraverso questo esempio, scopriremo i passaggi chiave e le best practice per applicare il metodo SMED in contesti produttivi diversi.
La sfida: tempi di set-up troppo lunghi
La vetreria oggetto del nostro studio produce bottiglie e contenitori per diversi settori, gestendo oltre 200 referenze attive. Questa varietà implica cambi formato frequenti, ciascuno dei quali richiede la sostituzione di stampi, regolazioni tecniche e verifiche di qualità.
Prima dell’intervento, la situazione evidenziava diverse criticità legate ai tempi di set-up che incidevano negativamente sulla produttività complessiva. Il tempo medio per completare un cambio formato era di circa 4 ore, una durata significativa che comportava frequenti interruzioni nei cicli di produzione. Con una media di 5 cambi formato giornalieri, si arrivava a un totale di 20 ore di inattività a settimana, equivalente a quasi tre intere giornate lavorative perse solo per attività di set-up. Questi tempi morti si traducevano non solo in inefficienze operative, ma anche in costi indiretti elevati, sia in termini di energia e risorse sprecate che di mancata produzione.
Inoltre, la lentezza del processo contribuiva a generare scarti, poiché le attrezzature non erano ottimizzate per il rapido passaggio da un formato all’altro, aumentando il margine di errore. Queste problematiche si riflettevano anche sulla capacità dell’azienda di rispettare le tempistiche di consegna, mettendo a rischio la soddisfazione dei clienti e la competitività sul mercato. La complessità del processo rendeva il set-up un ostacolo significativo per la produttività e i costi operativi.
Soluzione: ridurre drasticamente i tempi di set-up con il metodo SMED
CROSSNOVA ha applicato la metodologia SMED attraverso un processo in quattro fasi, che ha trasformato il set-up da un’attività lunga e dispersiva a un procedimento rapido e standardizzato.
Analisi delle attività di set-up
Il team ha mappato tutte le attività di set-up, distinguendo tra:
- Operazioni interne: eseguibili solo a macchina ferma.
- Operazioni esterne: eseguibili con la macchina in funzione.
Dall’analisi è emerso che il 70% delle attività veniva gestito come operazioni interne, sebbene molte potessero essere convertite in operazioni esterne.
Separazione e ottimizzazione delle attività esterne
Le attività esterne sono state riorganizzate per ridurre il tempo macchina fermo:
- Gli stampi sono stati preparati in una stazione dedicata, con strumenti preconfigurati.
- Carrelli attrezzati con tutto il necessario per il cambio formato hanno velocizzato il trasporto e l’installazione.
Miglioramento delle attività interne
Le operazioni interne sono state rese più rapide e precise:
- Sono stati introdotti sistemi di aggancio rapido per gli stampi, riducendo il tempo di sostituzione da 40 minuti a 15 minuti.
- Indicatori visivi e modelli di riferimento hanno minimizzato errori e ritardi.
Standardizzazione e formazione
Sono state create checklist operative per guidare gli operatori e garantire l’uniformità del processo. Inoltre, il personale è stato formato per eseguire le nuove procedure in modo rapido ed efficace.
I risultati: numeri che parlano chiaro
L’adozione della metodologia SMED ha generato miglioramenti significativi:
- Tempo medio di set-up: ridotto da 4 ore a 1,5 ore.
- Aumento della produttività: +20%, con un incremento del tempo di produzione effettivo da 80 a 96 ore settimanali.
- Riduzione degli scarti: set-up più precisi hanno diminuito gli errori e i difetti.
- Risparmio economico annuale stimato: oltre 50.000 euro.
Perché SMED è una strategia vincente per ridurre drasticamente i tempi di set-up
La metodologia SMED si è rivelata un game changer per questa vetreria. La riduzione dei tempi di set-up ha permesso all’azienda di aumentare l’efficienza, ridurre gli sprechi e rispondere più rapidamente alle esigenze del mercato.
Vuoi migliorare la produttività della tua azienda e apprendere come ridurre i tempi di set-up con il metodo SMED? Con la metodologia SMED, possiamo aiutarti a trasformare la tua produzione in un vantaggio competitivo. Contattaci subito!