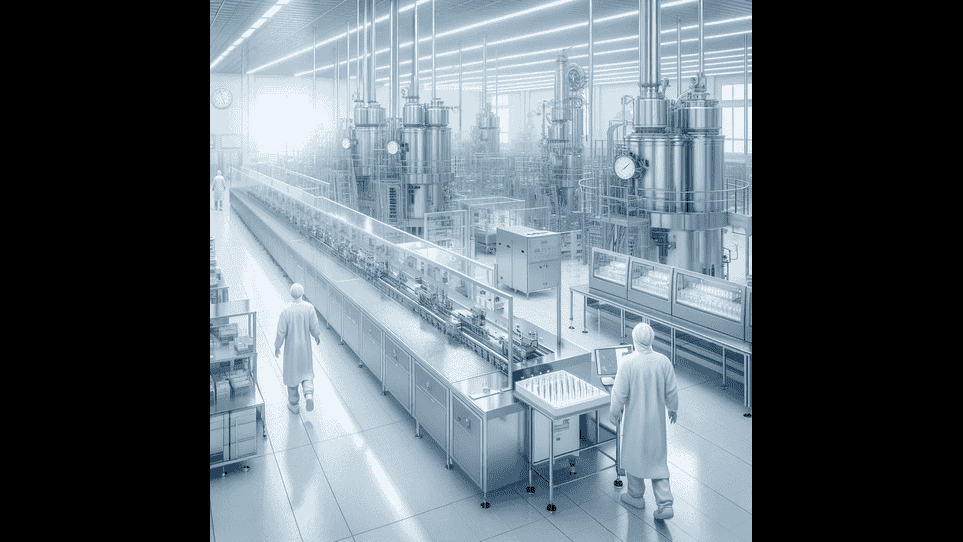
Ottimizzazione del processo di incollaggio ago nel settore farmaceutico: riduzione scarti con il metodo Lean Six Sigma
Il settore farmaceutico si trova costantemente di fronte alla sfida di garantire elevati standard di qualità e sicurezza. Questo obiettivo può essere raggiunto tramite la riduzione degli scarti con il metodo Lean Six Sigma. Uno degli aspetti critici nella produzione di dispositivi medici, come le siringhe, è l’incollaggio degli aghi. Questa operazione richiede precisione e accuratezza per evitare difetti che possono compromettere la funzionalità del prodotto finale.
- Per affrontare questa problematica, una nota multinazionale farmaceutica ha applicato il metodo Lean Six Sigma. Il metodo è una combinazione di strumenti Lean, per eliminare sprechi e attività a non valore aggiunto, e di Six Sigma, per ridurre la variabilità nei processi. Il metodo ha consentito di migliorare la qualità complessiva e ridurre i costi associati agli scarti.
- In questo use case esamineremo come il Lean Six Sigma possa essere implementato con successo per ottimizzare il processo di incollaggio ago nel settore farmaceutico, riducendo gli scarti. La metodologia segue le fasi DMAIC (Definire, Misurare, Analizzare, Migliorare, Controllare), adottando un approccio metodico e basato sui dati.
Definire: identificazione del problema e degli obiettivi
La fase iniziale è cruciale per stabilire una comprensione chiara e condivisa del problema. In questo caso, il problema centrale riguarda l’alto tasso di scarti nel processo di incollaggio degli aghi per siringhe. Questa è una fase critica nel settore farmaceutico dove precisione e conformità ai requisiti normativi sono essenziali. Il tasso di difettosità del processo si misura in base al numero di aghi scartati rispetto al totale prodotto. Inizialmente, si attestava su un valore medio del 15%, ben oltre il livello accettabile per il settore che si posiziona attorno al 5%.
Questo tasso di scarto elevato comporta non solo un incremento dei costi operativi, ma anche ritardi nelle consegne. Questo tasso di scarto ha un impatto significativo sul rendimento dell’intera linea di produzione. Si stima che i costi legati agli scarti ammontino a circa 500.000 € all’anno, rappresentando una parte sostanziale dei costi di produzione totali. Inoltre, ogni lotto difettoso non solo influisce sulla produttività, ma aumenta anche il rischio di non conformità ai requisiti di sicurezza e regolatori. I difetti possono causare potenzialmente richiami di prodotto, con costi aggiuntivi e danni reputazionali.
Obiettivo primario
L’obiettivo principale è la riduzione del tasso di difettosità nel processo di incollaggio degli aghi del 50% entro un periodo di sei mesi. Ciò significa che il tasso di scarti dovrà passare dall’attuale 15% a un massimo del 7,5%, con un miglioramento tangibile delle performance. Il tutto dovrà essere realizzato mantenendo costanti gli standard di qualità farmaceutici. Essi prevedono conformità rigorose alle normative internazionali (come GMP – Good Manufacturing Practices) e ai requisiti delle autorità di regolamentazione come FDA e EMA.
Obiettivi secondari
Oltre all’obiettivo primario, abbiamo definito i seguenti obiettivi secondari, sempre misurabili e legati a performance specifiche:
- Ridurre i costi legati agli scarti del 25%: Questo significa un risparmio di circa 125.000 € all’anno. Il risparmio si ottiene attraverso una diminuzione diretta degli scarti, evitando sprechi di materiali come aghi, adesivi e tempo macchina, oltre alla riduzione del lavoro legato alla gestione dei lotti difettosi
- Migliorare il tempo ciclo del processo del 10%: Attualmente, il tempo ciclo per il completamento di un lotto di siringhe è in media di 4 ore. L’obiettivo è ridurre questo tempo a 3,6 ore, tramite l’eliminazione di passaggi non necessari, un migliore bilanciamento delle attività e la riduzione dei tempi di inattività causati da arresti per problemi legati agli scarti
- Stabilizzare la variabilità del processo: Uno degli obiettivi fondamentali del progetto è ridurre la variabilità dei parametri critici di processo (CTQ – Critical to Quality), come la quantità di adesivo applicato, il tempo di adesione e la temperatura dell’ambiente di incollaggio. Attualmente, la variabilità misurata in termini di Cpk (Capability Process Index) si attesta a 1,2. Quest’ultimo indica un livello di qualità accettabile ma non ottimale. L’obiettivo è portare questo valore a 1,5, migliorando significativamente la capacità del processo di rimanere all’interno dei limiti di specifica senza generare scarti
Team e struttura del progetto
Il Team CROSSNOVA ha gestito il Progetto, seguendo i rigorosi principi Lean Six Sigma, con una struttura organizzativa ben definita per garantire l’efficacia delle azioni. Il team definito è multidisciplinare e comprende:
- Ingegneri di Produzione: Responsabili di analizzare i dati di processo e implementare modifiche tecniche per migliorare l’efficienza e la qualità
- Operatori di Linea: Figure chiave per l’operatività quotidiana del processo, essenziali nel fornire feedback sulle condizioni reali della produzione e nell’implementare soluzioni pratiche
- Responsabili della Qualità: Esperti che assicurano che le soluzioni implementate rispettino i rigorosi standard di qualità farmaceutici e normativi, oltre a monitorare le performance del processo in termini di difettosità
- Statistici e Analisti dei Dati: Sono responsabili dell’elaborazione dei dati raccolti e dell’analisi statistica, inclusa l’identificazione di trend e variazioni, e la validazione delle soluzioni implementate attraverso test quantitativi
Project Charter e KPI
Una parte essenziale della fase di definizione è stata la stesura del Project Charter, per delineare il problema, gli obiettivi, i tempi e i ruoli del team. In questo caso, Crossnova ha ufficializzato i seguenti elementi:
- Descrizione del problema: Elevato tasso di scarti e difettosità nel processo di incollaggio degli aghi, con un impatto sui costi e sulle tempistiche di consegna.
- Obiettivi specifici: Riduzione del tasso di difettosità del 50%, riduzione dei costi del 25%, miglioramento del tempo ciclo del 10%, aumento del Cpk a 1,5.
- Cronoprogramma: Suddiviso in fasi DMAIC (Define, Measure, Analyze, Improve, Control), con un piano temporale dettagliato. Ad esempio, la fase di Misura sarà completata entro il primo mese, mentre la fase di Implementazione delle soluzioni avverrà entro i primi tre mesi.
- KPI (Key Performance Indicators): Metriche chiave che il team monitorerà costantemente per valutare il progresso del progetto. Alcuni KPI includono:
- Tasso di difettosità: Da misurare settimanalmente, con un obiettivo di riduzione lineare che passa dal 15% iniziale al 7,5% in sei mesi
- Costo degli scarti: Riduzione progressiva dei costi legati agli scarti, con un obiettivo di risparmio annuale di 125.000 €
- Tempo ciclo: Misurazione del tempo medio di produzione per ogni lotto, con un obiettivo di riduzione a 3,6 ore per lotto
- Cpk: Monitoraggio della capability del processo, con obiettivo di miglioramento da 1,2 a 1,5 entro la fine del progetto
Misurare: raccolta dati e comprensione del processo
La fase di misurazione, tipicamente, è una delle più critiche nell’approccio Lean Six Sigma. Essa fornisce la base quantitativa su cui si basano tutte le analisi successive. In questa fase, il team si concentra sulla raccolta di dati accurati e dettagliati relativi al processo di incollaggio degli aghi per siringhe, identificando tutte le fonti di variabilità e i punti deboli che contribuiscono agli scarti.
Mappatura del processo con il Value Stream Mapping (VSM)
Il primo passo è stato quello di creare una mappa del flusso di valore (Value Stream Mapping – VSM) per ottenere una visione completa del processo di produzione. Questo strumento ha permesso di identificare le fasi a valore aggiunto e quelle che invece rappresentano potenziali sprechi. Il VSM ha rivelato che il processo di incollaggio degli aghi include sette fasi principali:
- Preparazione del materiale: Prelievo dell’adesivo e degli aghi da magazzino
- Dosaggio dell’adesivo: Applicazione dell’adesivo sulla siringa
- Assemblaggio ago-siringa: Inserimento dell’ago nella siringa
- Polimerizzazione dell’adesivo: Attesa per la completa adesione e solidificazione dell’adesivo
- Controllo qualità manuale: Verifica visiva dell’integrità dell’incollaggio
- Imballaggio del prodotto: Inserimento delle siringhe conformi nelle confezioni
- Stoccaggio: Trasferimento delle siringhe imballate al magazzino per la distribuzione
Attraverso questa mappatura, abbiamo identificato alcuni punti critici di inefficienza. Ad esempio, si è osservato che il tempo medio del ciclo di polimerizzazione era 30 minuti, con una variazione del 15% tra i diversi lotti, dovuta principalmente a condizioni ambientali non controllate. Inoltre, l’errore umano durante il dosaggio e il controllo qualità manuale sono stati individuati come fonti di variabilità e sprechi.
Raccolta dei dati quantitativi
Abbiamo eseguito la raccolta dei dati quantitativi mediante un sistema di monitoraggio automatizzato, ove possibile, e con dei piani di campionamento manuali. I principali dati raccolti includono:
- Tasso di difettosità: Il team ha analizzato il numero di aghi difettosi rispetto al totale prodotto in diversi turni e condizioni operative. In media, il tasso di scarti risultava essere del 15%, con punte di 20% in condizioni di elevata umidità o temperature non controllate.
- Quantità di adesivo applicata: Utilizzando un sistema di misurazione in linea, il dosaggio dell’adesivo è stato monitorato. La quantità ottimale di adesivo applicato è stata determinata in 0,07 ml per ago, ma la variabilità riscontrata variava dal -10% al +15%, a seconda della calibrazione del dosatore e della frequenza di manutenzione della macchina.
- Tempo ciclo di polimerizzazione: Come precedentemente indicato, il tempo di polimerizzazione previsto era di 30 minuti, ma i dati hanno rivelato variazioni tra 25 e 35 minuti a causa di fluttuazioni di temperatura e umidità nell’ambiente produttivo.
- Dimensioni dell’ago: L’8% degli aghi non rientrava nelle tolleranze dimensionali previste (±0,02 mm di diametro), influenzando negativamente l’adesione con la siringa.
Identificazione delle principali cause di difettosità
Durante questa fase, è stato fondamentale individuare le principali cause che influenzavano il tasso di difettosità. Oltre agli scarti legati alla variabilità nel dosaggio dell’adesivo e alle dimensioni dell’ago, altri fattori critici sono emersi:
- Errata applicazione dell’adesivo: Dai dati raccolti, si è osservato che il 40% dei difetti era dovuto a una quantità inadeguata di adesivo, con casi di applicazione insufficiente che causavano scarsa adesione, e casi di eccesso di adesivo che portavano a fuoriuscite e contaminazioni.
- Non conformità nelle dimensioni dell’ago: Le variazioni dimensionali dell’ago, misurate tramite calibri digitali, hanno mostrato che aghi fuori tolleranza (±0,02 mm) compromettevano l’incollaggio, con un tasso di difettosità che aumentava fino al 30% nei lotti con dimensioni non conformi.
- Condizioni ambientali non ottimali: La temperatura e l’umidità hanno avuto un impatto significativo sul processo di polimerizzazione dell’adesivo. L’analisi dei dati ambientali ha rilevato che una temperatura superiore a 25°C o un’umidità relativa superiore al 60% aumentavano il tempo di polimerizzazione e il rischio di difettosità. In queste condizioni, il tasso di difettosità aumentava di circa il 20% rispetto ai lotti prodotti in ambienti controllati.
Analisi della capacità del processo: Capability Analysis
Per valutare la capacità del processo di incollaggio di soddisfare le specifiche richieste, è stato eseguito un Capability Analysis. Il parametro critico misurato è stato la forza di adesione tra ago e siringa, che doveva rientrare in un range di 30-45 MPa. Tuttavia, i dati raccolti hanno mostrato che il 10% dei lotti non soddisfaceva questo criterio, con una forza media di adesione inferiore ai 28 MPa in condizioni di umidità elevata.
Il Process Capability Index (Cpk), utilizzato per valutare la capacità del processo di operare entro i limiti di specifica, era inizialmente di 1,2, indicativo di un processo che operava vicino ai limiti di tolleranza, ma con una significativa variabilità. L’obiettivo del progetto è portare questo valore a 1,5, riducendo così il numero di lotti non conformi.
Analisi Gage R&R (Repeatability and Reproducibility)
Per garantire che gli strumenti di misura utilizzati nel monitoraggio del processo fossero accurati e affidabili, è stata condotta un’analisi Gage R&R. Questo test valuta sia la ripetibilità (quanto uno strumento fornisce risultati consistenti quando utilizzato dallo stesso operatore) sia la riproducibilità (quanto i risultati variano quando l’operatore cambia).
Il Gage R&R ha rivelato che la variabilità dovuta agli strumenti di misurazione rappresentava circa il 5% della variabilità totale del processo, un valore accettabile. Tuttavia, abbiamo riscontrato alcuni problemi di ripetibilità nel sistema di dosaggio dell’adesivo, con differenze significative tra gli operatori durante i turni. Questo problema ha contribuito ad aumentare la variabilità complessiva del dosaggio fino a 10% tra i diversi operatori.
Questa fase di misurazione ha fornito una chiara comprensione delle variabili chiave del processo e delle principali fonti di variabilità che contribuivano agli scarti. I dati raccolti hanno costituito la base per l’analisi successiva, permettendo al team di focalizzarsi sulle aree che avrebbero avuto il maggiore impatto nel migliorare la qualità del processo e nel ridurre i difetti.
Analizzare: identificazione delle cause radice
Una volta completata la fase di misurazione e raccolti i dati quantitativi relativi al processo, il team, guidato da Crossnova, si è concentrato sull’analisi dettagliata per individuare le cause radice che contribuiscono agli scarti nel processo di incollaggio degli aghi. Questa analisi è essenziale per assicurarsi che gli interventi di miglioramento siano mirati a eliminare le fonti primarie di difettosità e non sintomi superficiali.
Per facilitare questo processo, è stata condotta una prima analisi tramite il diagramma di Ishikawa (o diagramma a spina di pesce), che permette di organizzare le potenziali cause di un problema in categorie chiave: Materiali, Metodo, Macchine, Manodopera, Ambiente e Misura. Questo approccio strutturato consente di esaminare tutti gli aspetti del processo in modo olistico e di identificare le cause radice più probabili.
Categorie e cause principali
1. Macchine
- Macchinari non calibrati correttamente: I dati raccolti nella fase di misurazione hanno evidenziato che la variazione nel dosaggio dell’adesivo era significativamente influenzata da una calibrazione inadeguata dei macchinari. I test eseguiti hanno rivelato che i dosatori, se non calibrati settimanalmente, possono deviare dal valore ottimale fino al 15% nel volume di adesivo erogato, con conseguente applicazione insufficiente o eccessiva di adesivo. Ciò si è tradotto in un aumento del 30% dei difetti nelle siringhe nei lotti prodotti con dosatori non calibrati regolarmente.
- Usura dei componenti: L’usura degli ugelli degli applicatori di adesivo è stata un’altra causa identificata che influenzava la precisione del dosaggio. I dati di manutenzione predittiva hanno dimostrato che dopo un ciclo di 10.000 applicazioni, il livello di precisione scendeva significativamente, con una deviazione del 10-12% rispetto al dosaggio corretto.
2. Manodopera
- Operatori non adeguatamente formati: L’analisi dei turni ha mostrato che i lotti prodotti da operatori con meno esperienza tendevano a presentare un tasso di difettosità superiore del 20% rispetto ai lotti prodotti da personale esperto. La principale causa di questo aumento di difetti era dovuta a una manipolazione non corretta degli aghi e a una scarsa capacità di monitorare visivamente la quantità di adesivo applicato durante il processo manuale. Ciò è stato confermato attraverso audit interni e feedback diretti dagli operatori di linea.
- Errori manuali nel controllo qualità: Il controllo qualità manuale dell’incollaggio ha mostrato una variabilità del 5% nella capacità degli operatori di rilevare difetti minori. Questo limite è stato associato alla mancanza di una formazione continua, che ha portato a una diminuzione della precisione nel rilevamento dei difetti dopo lunghi turni di lavoro.
3. Materiali
- Adesivi non idonei: L’analisi della compatibilità tra l’adesivo e i materiali dell’ago e della siringa ha rivelato che circa il 10% degli scarti era dovuto a una scarsa adesione dell’ago, causata da incompatibilità chimiche tra l’adesivo e le superfici trattate termicamente degli aghi. I test di laboratorio hanno dimostrato che in condizioni di temperatura e umidità elevate, la forza di adesione dell’adesivo si riduceva del 20%, portando a un aumento della probabilità di fallimenti del processo.
- Qualità degli aghi: Dai dati raccolti, è emerso che il 8% degli aghi forniti dai fornitori non rispettava le tolleranze dimensionali (±0,02 mm), portando a una ridotta efficacia nell’incollaggio e un conseguente aumento del tasso di difettosità del 15% nei lotti in cui venivano utilizzati aghi non conformi.
4. Metodo
- Processo di polimerizzazione non ottimale: I dati raccolti durante la fase di misura hanno mostrato che le variazioni nel tempo di polimerizzazione dell’adesivo contribuivano significativamente agli scarti. In lotti in cui il tempo di polimerizzazione era inferiore ai 30 minuti, il tasso di difettosità aumentava di oltre il 25% rispetto ai lotti trattati con tempi di polimerizzazione adeguati. La principale causa di questa variabilità è stata attribuita alla mancanza di controllo rigoroso sulla temperatura e l’umidità nelle aree di produzione.
5. Ambiente
- Condizioni ambientali non controllate: L’analisi dei dati ambientali ha confermato che un’elevata umidità (>60%) e temperature superiori ai 25°C influenzavano negativamente il processo di polimerizzazione dell’adesivo, portando a un incremento del 20% nel tasso di difettosità. Questi dati sono stati raccolti tramite sensori di monitoraggio installati nelle aree di produzione e confrontati con i lotti prodotti in condizioni ambientali ottimali. La mancanza di un sistema di controllo ambientale in alcune fasi della produzione è stata identificata come una causa radice importante da affrontare.
6. Misura
- Strumenti di misurazione non adeguati: L’analisi Gage R&R condotta nella fase precedente ha rivelato che la precisione degli strumenti di misura utilizzati per il controllo del dosaggio e delle dimensioni degli aghi contribuiva alla variabilità del processo. In particolare, i calibri utilizzati per misurare le dimensioni degli aghi presentavano una variabilità del 5%, aumentando la probabilità di accettare aghi fuori specifica.
Conferma delle cause radice tramite Design of Experiments (DOE)
Per verificare l’impatto di queste cause radice identificate, il team ha condotto una serie di esperimenti utilizzando il Design of Experiments (DOE). Questo approccio statistico ha permesso di isolare e testare le variabili critiche per valutare il loro effetto sulla qualità finale del prodotto e, in particolare, sul tasso di difettosità.
Nel DOE sono state testate le seguenti variabili:
- Pressione di dosaggio dell’adesivo: Tre livelli di pressione (0,5 bar, 0,7 bar, 1,0 bar) sono stati testati per verificare l’effetto sulla quantità di adesivo applicata e sulla forza di adesione
- Tempo di polimerizzazione: Sono stati testati tre tempi (25 minuti, 30 minuti, 35 minuti) per valutare la corretta polimerizzazione dell’adesivo in diverse condizioni ambientali
- Temperatura e umidità: Le condizioni ambientali sono state controllate in un range di temperature tra 20°C e 30°C, e umidità tra 40% e 70%, per determinare l’impatto sull’efficienza dell’adesivo
I risultati del DOE hanno confermato che la pressione di dosaggio ottimale era 0,7 bar, con un tempo di polimerizzazione ideale di 30 minuti e condizioni ambientali controllate a 22°C e umidità 50%. Questi parametri hanno ridotto il tasso di difettosità del 40% nei lotti sperimentali, validando le ipotesi sulle cause radice.
Questa analisi approfondita ha permesso di identificare con precisione i fattori chiave che influenzano la qualità del processo di incollaggio e di fornire una solida base per implementare miglioramenti mirati nella fase successiva.
Migliorare: sviluppo e implementazione delle soluzioni
Dopo aver completato con successo l’analisi delle cause radice nella fase precedente e aver validato le ipotesi tramite il Design of Experiments (DOE), il team si è dedicato all’implementazione delle soluzioni per ridurre significativamente il tasso di difettosità del processo di incollaggio degli aghi.
Ottimizzazione del dosaggio dell’adesivo
Una delle cause principali di difettosità riscontrata era la variabilità nel dosaggio dell’adesivo, influenzata dalla pressione e dal tempo di applicazione. Grazie all’analisi DOE condotta nella fase precedente, il team ha determinato che i parametri ottimali per la pressione del dosatore erano 0,7 bar, con un tempo di applicazione di 1,0 secondo e una quantità di adesivo di 0,07 ml per ago. Questi parametri sono stati implementati in tutta la linea di produzione, riducendo la variabilità del dosaggio e abbassando il tasso di difettosità del 40% rispetto ai lotti precedenti.
La nuova configurazione è stata monitorata attraverso sensori di pressione in tempo reale, integrati nel sistema di controllo qualità del processo. Questo ha permesso un intervento immediato in caso di deviazioni, con una conseguente riduzione del margine di errore nel dosaggio a meno del 5%.
Calibrazione regolare delle apparecchiature
Come emerso dall’analisi delle cause radice, la mancata calibrazione regolare delle apparecchiature di dosaggio contribuiva significativamente alla variabilità del processo. Per risolvere questo problema, abbiamo introdotto un protocollo di calibrazione settimanale per tutte le macchine applicatrici di adesivo. I dati raccolti nella fase di misura avevano mostrato che, senza calibrazioni frequenti, la deviazione nel dosaggio poteva raggiungere fino al 15%. Con la nuova procedura di calibrazione, la deviazione è stata ridotta a 3%, migliorando significativamente la stabilità del processo.
Inoltre, abbiamo implementato una manutenzione predittiva basata sui dati di utilizzo delle macchine, che ha permesso di identificare e sostituire tempestivamente componenti critici soggetti a usura, come gli ugelli di erogazione. Ciò ha ulteriormente contribuito a mantenere il processo stabile e sotto controllo.
Formazione degli operatori
Un’altra causa radice identificata era legata alla mancanza di formazione adeguata degli operatori, che portava a errori manuali e a un tasso di difettosità elevato, soprattutto durante i cambi turno. Per risolvere questa problematica, abbiamo sviluppato un programma di formazione specifico che includeva sessioni teoriche e pratiche. Il programma si concentrava su:
- Tecniche di manipolazione degli aghi e delle siringhe per ridurre il rischio di danneggiamenti e difetti durante l’incollaggio.
- Uso corretto delle apparecchiature di dosaggio e delle tecnologie di controllo qualità.
- Conoscenze sull’importanza della conformità alle specifiche di processo, con l’obiettivo di ridurre gli errori umani nel controllo qualità manuale.
La formazione ha portato a una riduzione del 20% del tasso di difettosità legato agli errori umani, con un miglioramento nella precisione delle operazioni di incollaggio e controllo qualità. Inoltre, gli operatori hanno dimostrato una maggiore capacità di rilevare difetti minori durante i controlli visivi, migliorando ulteriormente la qualità del prodotto.
Sostituzione dell’adesivo
L’analisi delle cause radice aveva evidenziato problemi di compatibilità tra l’adesivo utilizzato e i materiali degli aghi e delle siringhe, specialmente in condizioni ambientali non ottimali. A seguito di test approfonditi, abbiamo selezionato un nuovo adesivo epossidico, più performante e meno sensibile a variazioni di temperatura e umidità.
I test eseguiti con il nuovo adesivo hanno mostrato un incremento della forza di adesione del 25% in condizioni ambientali estreme, riducendo il tasso di difettosità legato a scarse adesioni dal 20% al 5%. Questo ha permesso di standardizzare il processo di incollaggio e garantire risultati più consistenti anche durante periodi di elevata umidità o temperature più alte nella sala di produzione.
Implementazione del sistema 5S
Oltre agli interventi tecnici, il team ha implementato un sistema 5S (Sort, Set in order, Shine, Standardize, Sustain) per migliorare l’organizzazione e la pulizia delle postazioni di lavoro. Nella fase di analisi, una postazione disorganizzata contribuiva a ritardi nei tempi ciclo e aumentava la probabilità di errori umani e contaminazioni.
L’applicazione del sistema 5S ha portato a:
- Riduzione dei tempi di attrezzaggio del 30%, grazie a un’organizzazione più efficiente degli strumenti e dei materiali.
- Riduzione delle contaminazioni del 15%, grazie a una maggiore pulizia e ordine delle aree di lavoro.
- Maggiore efficienza complessiva del processo, con una riduzione del tempo ciclo del 10%.
L’introduzione del sistema 5S ha inoltre migliorato la motivazione e la consapevolezza degli operatori, che hanno sviluppato una maggiore attenzione verso la qualità e la pulizia del processo.
Controllare: monitoraggio e sostenibilità dei miglioramenti
La fase finale del ciclo DMAIC, “Controllare”, è essenziale per garantire che i miglioramenti ottenuti siano sostenibili nel tempo e che il processo di incollaggio degli aghi continui a funzionare entro i parametri stabiliti. In questa fase, Crossnova ha suggerito di implementare un sistema di monitoraggio continuo per rilevare in modo tempestivo eventuali scostamenti dal processo ottimizzato, prevenendo così il ritorno a livelli di difettosità elevati.
Implementazione di Control Chart
Uno degli strumenti principali utilizzati in questa fase è il Control Chart, che consente di monitorare costantemente le variabili chiave del processo, come la quantità di adesivo applicata, il tempo di polimerizzazione e la temperatura ambientale. Questo strumento visualizza in tempo reale la variabilità del processo, permettendo di identificare rapidamente quando i parametri operativi si avvicinano ai limiti di tolleranza.
L’implementazione di Control Chart ha consentito di mantenere il Cpk a 1,6, un miglioramento significativo rispetto al valore di 1,2 osservato all’inizio del progetto. Il monitoraggio continuo della variabilità del processo ha permesso di ridurre ulteriormente i difetti legati a deviazioni minime dai parametri ottimali, con un impatto positivo sulla qualità del prodotto finale.
Standard Operating Procedures (SOP) e manutenzione preventiva
Per assicurare la sostenibilità dei miglioramenti nel lungo termine, il team ha anche sviluppato e implementato nuove Standard Operating Procedures (SOP). Questi documenti normativi descrivono in dettaglio tutte le fasi operative del processo di incollaggio degli aghi, garantendo il rispetto delle procedure ottimizzate definite durante il progetto. Le SOP includono:
- I parametri specifici per il dosaggio dell’adesivo.
- Le istruzioni per il controllo delle condizioni ambientali.
- Le linee guida per l’ispezione manuale e automatica del prodotto finito.
In aggiunta alle SOP, sono stati implementati protocolli di manutenzione preventiva per assicurarsi che tutte le apparecchiature di produzione, soprattutto i dosatori di adesivo, vengano calibrate e mantenute in modo regolare. Grazie a queste misure, i macchinari funzionano costantemente entro i parametri ottimali, riducendo i tempi di inattività non programmata e mantenendo la qualità del prodotto stabile nel tempo.
Audit periodici e feedback dagli operatori
Un altro elemento chiave della fase di controllo è l’implementazione di audit periodici. Il team di qualità conduce questi audit, con il supporto degli ingegneri di processo, per verificare la correttezza esecuzione di tutte le procedure e la stabilità delle condizioni operative. Gli audit consentono di individuare eventuali deviazioni prima che possano causare problemi significativi.
Inoltre, il feedback continuo dagli operatori di linea gioca un ruolo essenziale nel mantenimento dei miglioramenti. Gli operatori sono stati formati per identificare potenziali segnali di deterioramento del processo e riportarli al team di ingegneria e qualità. Questo approccio proattivo permette di intervenire rapidamente, risolvendo problemi prima che possano compromettere il processo.
Risultati e conclusioni
L’implementazione del progetto Lean Six Sigma per ridurre gli scarti nel processo di incollaggio degli aghi ha portato a risultati concreti e significativi. Gli scarti sono stati ridotti del 55%, superando l’obiettivo iniziale del 50%, e i costi associati agli scarti sono stati ridotti del 30%, con un risparmio complessivo di 150.000€ all’anno. Questi miglioramenti hanno avuto un impatto positivo sui costi e sull’efficienza complessiva della produzione. Hanno anche migliorato la capacità di rispettare i tempi di consegna.
Uno dei risultati più importanti è stato il miglioramento della stabilità del processo. La variabilità è stata ridotta in modo significativo, e il processo ora opera con un Cpk di 1,6, ben oltre il valore di 1,2 all’inizio del progetto. Questo livello di controllo assicura che il processo possa continuare a produrre siringhe conformi agli standard di qualità richiesti dal settore farmaceutico, con una riduzione delle difettosità complessive al 5,5%, ben al di sotto dell’obiettivo prefissato del 7,5%.
In conclusione, l’approccio Lean Six Sigma si è dimostrato una strategia vincente per migliorare sia l’efficienza che la qualità del processo di incollaggio degli aghi. Attraverso l’uso di strumenti Lean per l’eliminazione degli sprechi e Six Sigma per la riduzione della variabilità, il team è riuscito a trasformare un processo problematico in uno stabile e controllato.
Questo progetto è un esempio di come un’analisi sistematica dei processi e l’implementazione di soluzioni basate sui dati possano generare benefici tangibili. I benefici si traducono non solo in una riduzione dei costi, ma anche di affidabilità e soddisfazione del cliente. Grazie all’attenzione costante al Miglioramento Continuo e al coinvolgimento degli operatori di linea, l’azienda è ora in grado di mantenere un processo produttivo di alta qualità. Ciò consente di continuare a crescere in un mercato altamente competitivo come quello farmaceutico.
Se anche la tua azienda desidera ottimizzare i processi produttivi e ridurre gli sprechi, contattaci subito per saperne di più!