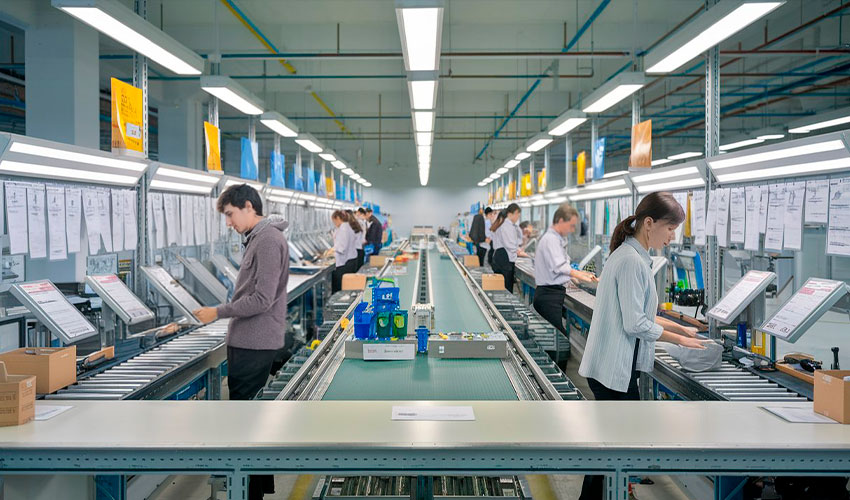
Lean Manufacturing: Significato e Definizione
Lean Manufacturing, noto anche come “produzione snella“, è un approccio alla gestione aziendale nato in Giappone negli anni ’50, grazie al sistema di produzione Toyota.
Il significato della lean manufacturing si estende oltre la semplice riduzione dei costi; infatti, coinvolge l’intera cultura aziendale promuovendo un ambiente di lavoro collaborativo e innovativo.
Lean si concentra sull’eliminazione degli sprechi e sul miglioramento continuo per rendere l’azienda più efficiente e rispondere meglio alle esigenze dei clienti.
Il concetto di sprechi (in giapponese ‘muda’) è fondamentale nel Lean Manufacturing. In pratica, si tratta di qualsiasi attività che non aggiunge valore al prodotto o servizio finale.
Pensa, ad esempio, ai tempi morti mentre aspetti che una macchina completi il suo ciclo: tutto quel tempo è uno spreco che non offre alcun beneficio al cliente. Esistono sette tipi principali di sprechi nel Lean:
- Sovrapproduzione: produrre più di quanto richiesto.
- Attese: tempi morti nei processi.
- Trasporti Inutili: movimentazione eccessiva dei materiali.
- Processi in Eccesso: fasi di lavorazione non necessarie.
- Scorte: materiali accumulati in quantità superiori al necessario.
- Movimenti Inutili: spostamenti inutili da parte degli operatori.
- Difetti: errori che richiedono rilavorazioni.
Ridurre questi sprechi consente alle aziende di migliorare l’efficienza, ridurre i costi e aumentare la qualità.
Il Lean Manufacturing si fonda su alcuni principi fondamentali che aiutano a comprendere il suo significato pratico.
Principi del Lean Manufacturing:
- Valore dal punto di vista del cliente: Il punto di partenza è capire cosa rappresenta davvero valore per il cliente. In altre parole, cosa rende un prodotto o un servizio interessante e degno di essere pagato? Tutto ciò che non contribuisce direttamente a questo valore è considerato uno spreco e dovrebbe essere eliminato.
- Mappatura del Flusso di Valore: Questo principio si riferisce all’analisi di tutte le attività coinvolte nel portare un prodotto o servizio al cliente, per identificare quali aggiungono valore e quali rappresentano sprechi.
- Flusso Continuo: Una volta eliminati gli sprechi, l’obiettivo è creare un flusso produttivo senza interruzioni, riducendo i tempi di attesa e migliorando l’efficienza.
- Produzione Pull: Nel sistema Lean, la produzione avviene solo in risposta alla domanda del cliente, evitando sovrapproduzione e scorte eccessive.
- Miglioramento Continuo (Kaizen): Questo principio implica un processo continuo di miglioramento, che coinvolge tutti i dipendenti nell’individuazione di opportunità per ottimizzare il lavoro.
Un esempio pratico di Lean Manufacturing è il metodo “5S”, un sistema che aiuta a mantenere l’ordine e la pulizia sul posto di lavoro, rendendo tutto più efficiente e sicuro.
Pensa al tuo garage di casa: se ogni attrezzo è al suo posto, non perdi tempo a cercare ciò di cui hai bisogno.
Boeing ha utilizzato con successo il metodo 5S per organizzare le sue linee di produzione, risparmiando tempo e migliorando l’efficienza complessiva. Le 5S rappresentano cinque parole giapponesi che si riferiscono a passaggi specifici: Seiri (separare), Seiton (riordinare), Seiso (pulire), Seiketsu (standardizzare), e Shitsuke (sostenere).
Altri Strumenti e Tecniche del Lean Manufacturing
Kanban:
Un sistema di gestione visuale che aiuta a controllare il flusso dei materiali e delle informazioni all’interno del processo produttivo. Kanban utilizza schede per segnalare quando è necessario rifornire i materiali, evitando così la sovrapproduzione e le scorte eccessive.
JIT (Just-In-Time):
La produzione “Just-In-Time” mira a produrre solo ciò che è necessario, quando è necessario, e nella quantità necessaria. Questo approccio riduce al minimo le scorte e aiuta le aziende a rispondere rapidamente alle esigenze del cliente, riducendo i tempi di ciclo e migliorando la flessibilità.
Poka-Yoke:
Questa tecnica si basa sulla prevenzione degli errori e mira a progettare processi e strumenti che riducano al minimo la possibilità di commettere errori. Poka-Yoke si traduce in “a prova di errore” e contribuisce a migliorare la qualità del prodotto, riducendo al contempo i costi di scarto e rilavorazione.
Kaizen:
Il miglioramento continuo è uno dei pilastri del Lean Manufacturing. Il termine “kaizen” significa “cambiare in meglio” e implica il coinvolgimento di tutti i dipendenti nell’identificazione e nella risoluzione dei problemi. Il processo Kaizen può essere applicato a piccoli miglioramenti quotidiani o a progetti più grandi che mirano a trasformare intere aree dell’azienda.
Mappatura del Flusso di Valore (VSM):
La mappatura del flusso di valore è una tecnica che consente di visualizzare e analizzare ogni fase del processo produttivo, evidenziando le attività che aggiungono valore e quelle che rappresentano sprechi. Questo strumento aiuta a identificare opportunità di miglioramento e a ottimizzare il flusso dei materiali e delle informazioni.
Esempi Pratici di Implementazione del Lean Manufacturing
Toyota, come pioniere del Lean Manufacturing, ha implementato diverse pratiche Lean per ottimizzare la produzione. Il Toyota Production System (TPS) si basa su principi come JIT e Kanban, che consentono di ridurre al minimo gli sprechi e migliorare l’efficienza. Grazie all’approccio Lean, Toyota è diventata un punto di riferimento mondiale per la produzione snella.
Anche Nike ha adottato il Lean Manufacturing per migliorare l’efficienza delle sue operazioni. Attraverso l’uso di pratiche come il miglioramento continuo e la riduzione degli sprechi, Nike è riuscita a ridurre i tempi di produzione e a migliorare la qualità dei suoi prodotti, mantenendo al contempo l’impegno verso la sostenibilità.
Airbus ha utilizzato il Lean Manufacturing per ridurre i tempi di assemblaggio dei suoi aeromobili. Attraverso la mappatura del flusso di valore e l’implementazione del metodo 5S, Airbus è riuscita a identificare e ridurre le attività che non aggiungono valore, migliorando così l’efficienza operativa e riducendo i costi.
Come Implementare il Lean Manufacturing nella tua Azienda
Implementare il Lean Manufacturing significa cambiare il modo di pensare e lavorare di tutta l’azienda. Per superare le resistenze, è importante investire nella formazione, spiegare i benefici del Lean e coinvolgere tutti nel processo. Ad esempio, organizzare incontri informali in cui i dipendenti possano fare domande e proporre idee può aiutare molto.
Analizzare il flusso di valore è un passo fondamentale per identificare le attività che aggiungono valore e quelle che rappresentano sprechi.
È consigliabile iniziare con piccoli progetti pilota per testare l’efficacia degli strumenti Lean e creare fiducia nel processo. Applicare strumenti come 5S, Kanban e Kaizen contribuirà a migliorare gradualmente i processi e a rendere l’azienda più efficiente.
Monitorare costantemente i risultati e cercare sempre nuove opportunità di miglioramento è fondamentale per mantenere viva la cultura Lean.
Se desideri approfondire il Lean Manufacturing per la tua Azienda, scopri i nostri corsi:
Non perdere l’opportunità di accelerare la tua crescita professionale con strumenti pratici ed efficaci!