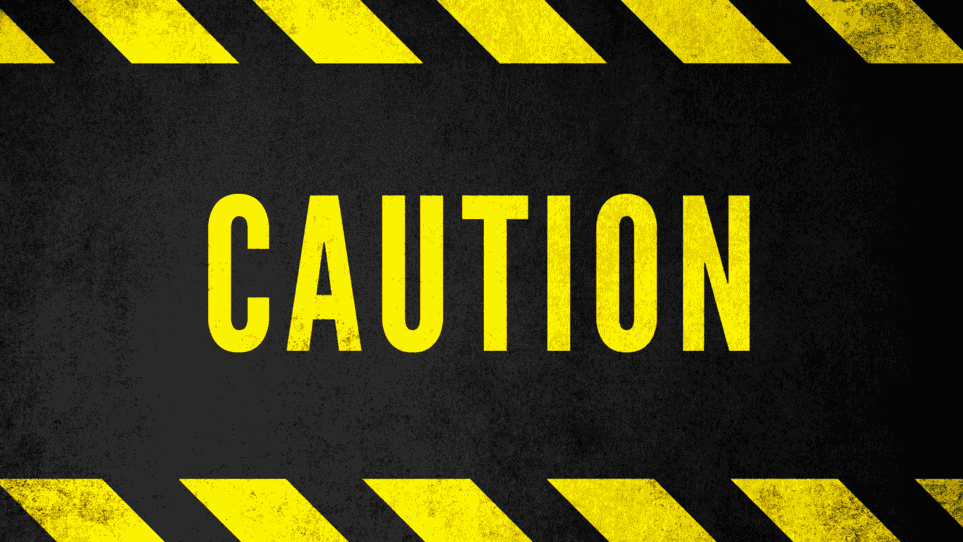
Guida in 7 step per la gestione delle non conformità
Misurare l’efficienza di una o più linee produttive o quella di un processo di business può rivelare una serie di non conformità con un impatto misurabile sulle performance di un’impresa. In uno scenario competitivo agguerrito, la gestione delle non conformità diventa un vero e proprio must. Non ci resta che capire in che modo.
Come gestire le non conformità in 7 step
Ecco perché risulta così cruciale la gestione delle non conformità in un ambiente complesso. Più anomalie si riescono a individuare, più si riuscirà a mantenere sotto controllo la riduzione delle variazioni di processo e i conseguenti rischi associati al business. In un intervento Lean Six Sigma la gestione della qualità e delle inefficienze che punta all’eliminazione delle non conformità diventa così uno strumento efficace per identificare e ridurre questi rischi. Di seguito guideremo il lettore in un percorso step by step per affrontare queste criticità in modo che ogni azienda sia in grado di analizzare la radice del problema, trovare una soluzione e prevedere eventi futuri.
Identificazione della non conformità
Una non conformità si riferisce a qualsiasi deviazione di processo da uno standard stabilito, sia questo un requisito interno, uno legale/normativo o una richiesta del cliente. Anche se gestita da una macchina, la ripetizione continua di un processo in una linea di produzione risulta per sua natura soggetta al fenomeno della variabilità, dando vita a discrepanze evidenti e misurabili tra le condizioni effettive di un prodotto a fine lavorazione e i requisiti definiti dagli standard di qualità. Le non conformità, se gestite nel modo sbagliato, possono generare gravi inefficienze, il tema è che non sempre sono così evidenti da essere intercettate con strumenti di uso quotidiano.
Se si scopre che la non conformità è dovuta a scarsa manutenzione, a un guasto delle macchine o delle attrezzature utilizzate sulla linea di produzione, allora l’attività deve essere immediatamente interrotta per permettere il ricondizionamento e la riparazione dell’apparecchiatura.
Il problema però è proprio capire dove si annida la non conformità e quali strumenti è possibile mettere in campo per individuarla. Molte fonti di variabilità possono apparire da subito evidenti già a una prima ispezione, mettendo a nudo le anomalie di esecuzione, come ad esempio: operatori che cercano l’attrezzatura giusta senza trovarla, strumenti conservati in posti sbagliati, persone non presenti quando c’è bisogno del loro intervento.
Altre volte invece sono necessari interventi più strutturali, come audit, segnalazioni effettuate da tecnici durante gli interventi di manutenzione e ispezioni programmate.
Segnalazione e documentazione
Per identificare e tracciare il prodotto o il processo non conforme è necessario registrare i suoi dati e da questi produrre una documentazione a supporto per l’analisi. Si prosegue quindi con l’integrazione delle informazioni in un’unica fonte: si possono implementare software specifici, oltre all’impiego del sistema MES, che da solo può aiutare a tenere traccia delle anomalie, identificarle e velocizzare l’intervento con azioni correttive.
Grazie all’integrazione di determinati moduli con focus verticale sulla risoluzione di problemi è possibile ottenere dati in tempo reale per individuare precocemente le non conformità e minimizzare il loro potenziale impatto.
È così, con il supporto di soluzioni tecnologiche, che le aziende aumentano l’agilità con cui prendono le decisioni sull’intervento ed eseguono più rapidamente le azioni correttive. In questo modo riducono in breve tempo i costi della “non qualità” rispettando la loro strategia di miglioramento continuo.
In questo senso, le tecnologie dell’industria 4.0 offrono grandi benefici. Si possono utilizzare sensori IoT, analisi dei dati con Intelligenza Artificiale e piattaforme di gestione della Qualità integrabili con applicativi aziendali.
Analisi delle cause
Questa fase è essenziale per evitare che la non conformità si ripresenti in futuro. Per individuare e affrontare la causa principale (che può essere una o più di una), esistono diverse metodologie utili, una di quelle più efficaci è lo strumento di analisi e risoluzione dei problemi detto dei “5 Perché”.
L’obiettivo di questo metodo analitico è porsi le domande giuste per arrivare a esplorare le ragioni profonde di un problema. Grazie a questa analisi si giunge a conclusioni più aderenti alle reali necessità di business.
Supportati da questo approccio, in Toyota arrivarono a capire che l’azienda non aveva bisogno di grandi scorte o di macchine specializzate, costose e difficili da personalizzare, quando invece le attrezzature di uso generale, tipicamente più piccole, erano meno costose, potevano produrre una più ampia varietà di pezzi ed erano facilmente riconfigurabili.
Azioni correttive e di remediation
La ISO 9001:2015 stabilisce una serie di misure da intraprendere quando viene rilevata una non conformità, una delle quali è l’applicazione di diverse azioni correttive. Una volta individuata la causa principale della non conformità, è necessario definire il da farsi.
Per garantire l’esecuzione del piano di intervento occorre in primis coinvolgere i responsabili di linea e stabilire delle tempistiche. Oltre alle misure da attuare per modificare direttamente i processi attraverso correzioni, semplificazioni e automatizzazioni, si possono mettere in pista altri interventi, come ad esempio:
- formare il personale;
- sostituire o riparare attrezzature obsolete o danneggiate;
- promuovere upgrade tecnologici;
- cambiare fornitori di materia prima;
- ottimizzare il layout degli impianti.
Verifica dell’efficacia
Tra le ultime fasi, questa è una delle più importanti perché servirà a capire se le azioni correttive implementate sono state efficaci o meno. Come è possibile saperlo? L’unico modo è attraverso una raccolta sul campo dei dati generati dai sistemi deputati al controllo. Non appena si presenta una situazione simile a quella che ha generato la non conformità occorre subito verificare che la deviazione non si verifichi più. Solo quando sarà possibile escludere al 100% il ripresentarsi della non conformità sarà possibile stabilire l’efficacia dell’azione correttiva e quindi chiudere definitivamente il problema.
Prevenzione delle recidive
Una chiave fondamentale per la gestione delle non conformità è la promozione di una cultura del miglioramento continuo. Ciò comporta la partecipazione attiva di tutti i dipendenti in chiave Lean all’identificazione, all’analisi e alla risoluzione delle non conformità.
La filosofia del miglioramento continuo dovrà incoraggiare il feedback e l’apprendimento organizzativo per evitare la ripetizione degli errori e promuovere l’innovazione dei processi.
Revisione e Miglioramento Continuo
Il rilevamento tempestivo e il continuo monitoraggio di una non conformità deve essere visto in realtà come un’opportunità di miglioramento. Se l’organizzazione dispone di un protocollo efficace come quello appena descritto per gestire queste situazioni potrà trarre vantaggio in realtà dalle variabilità di processo e sfruttarle a proprio favore come occasione per innovare.
Conclusione
Le non conformità sono strutturali a ogni processo di business. Operare un intervento di miglioramento per individuarle e gestirle è la cura migliore per il progresso, ma spesso si tende a considerare la variabilità solo come un problema. Al contrario, bisognerebbe imparare a considerarla anche come un’opportunità, uno stimolo per la generazione di nuove idee e modelli di business.
Scopri subito come applicare questi principi in azienda!