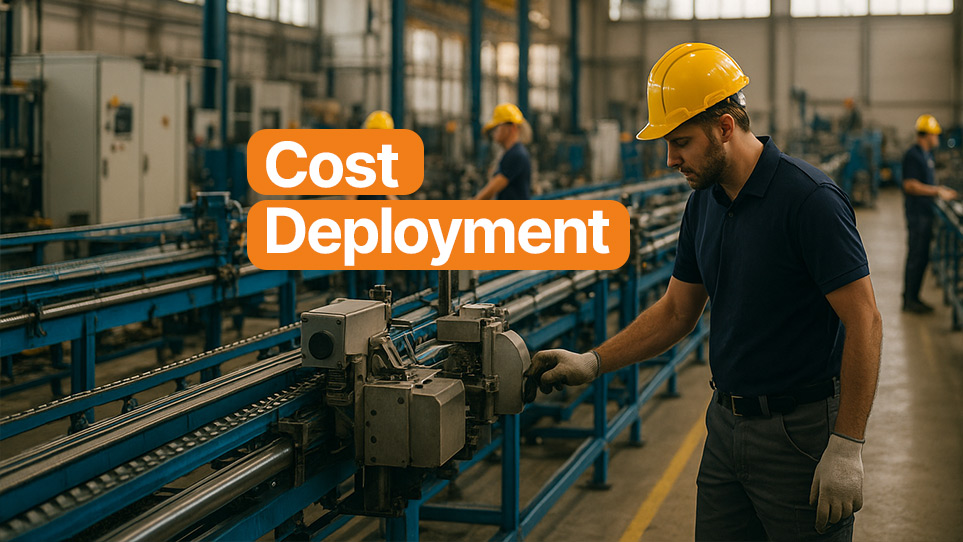
Cost deployment: il metodo lean per migliorare i margini aziendali
Nel 2024, un report di McKinsey ha rilevato che il 67% delle aziende ha visto i margini operativi contrarsi di 5 punti percentuali a causa dell’aumento dei costi energetici.
Il cost deployment offre una risposta sistematica a questo dilemma trasformando la gestione dei costi in un vero e proprio motore di creazione di vantaggio competitivo.
Che cos’è il cost deployment?
Il cost deployment affonda le sue radici nel Toyota Production System, ma ha evoluto gli insegnamenti Lean con l’introduzione di metodologie come il Lean Accounting negli anni 2000, che hanno esteso l’attenzione non solo ai processi produttivi, ma anche alla rendicontazione finanziaria per supportare decisioni strategiche basate sui flussi di valore reali.
A differenza di un taglio indiscriminato delle spese, questo metodo identifica e rimuove gli sprechi, riallocando risorse verso le attività che generano valore per il cliente. In pratica, il cost deployment connette la visione strategica di lungo termine con le operazioni quotidiane, integrando le analisi finanziarie con il miglioramento continuo dei processi.
La metodologia si distingue per l’approccio olistico: non si limita ai reparti di produzione, ma coinvolge vendite, logistica, manutenzione e persino ricerca e sviluppo. Ogni funzione contribuisce a identificare i cost driver, ossia le cause che determinano l’incidenza dei costi, permettendo un intervento mirato e coordinato.
Perché il cost deployment è essenziale
I costi nascosti legati a difetti, movimenti inutili e attese mostrano tutto il loro peso nel caso di un’azienda del settore elettronico, dove oltre il 15% del budget manutenzione era causato da fermi macchina evitabili.
Il cost deployment offre tre vantaggi chiave: innanzitutto favorisce la creazione di una cultura aziendale orientata al miglioramento continuo, in cui ogni collaboratore è incoraggiato a segnalare inefficienze. Inoltre traduce gli obiettivi finanziari in indicatori operativi chiari, riducendo il divario tra strategia e attività sul campo. Infine, grazie a un sistema di monitoraggio strutturato, i risultati non restano promesse, ma vengono misurati e consolidati nel tempo.
Ritornando all’impresa del settore elettronico, intervenendo su routine di check-list e diagnosi predittiva, ha ridotto i fermi del 40%, liberando risorse per attività di ricerca di nuovi prodotti.
Fase 1: analisi e mappatura iniziale
La prima fase si concentra sulla comprensione approfondita dei processi. Durante una sessione di Value Stream Mapping in un’azienda di componentistica elettronica, il team individuò un buffer di scorte tra due stazioni che generava ritardi di circa un’ora al giorno e costi di fermo macchina significativi.
Questa tecnica registra ogni fase del processo, dai tempi di ciclo alle giacenze di magazzino, fino ai movimenti e agli scarti, rivelando sprechi altrimenti invisibili. L’obiettivo è stabilire una baseline quantitativa e qualitativa che rifletta la reale situazione operativa.
Durante la mappatura, il team identifica i cost driver associando a ciascun elemento un valore economico. Un ritardo nella catena di approvvigionamento, per esempio, viene tradotto in costi di magazzino extra, mentre attività di riordino manuale continuo si trasformano in ore-uomo sprecate.
Il risultato è una fotografia nitida delle inefficienze più impattanti.
Fase 2: definizione delle opportunità e prioritizzazione
Analizzando le evidenze, il team ha optato per un intervento sul packaging: in un’azienda di ecommerce, la revisione dei materiali e del processo di imballo ha ridotto del 50% i resi, generando un risparmio di 200.000€ annui.
Il focus non è su tutto, ma sulle aree che generano ritorni significativi in tempi brevi. Il team valuta ogni proposta secondo criteri di impatto economico, complessità di implementazione e urgenza strategica.
Fase 3: progettazione e pianificazione delle azioni
Ogni iniziativa selezionata viene tradotta in un piano d’azione puntuale. Vengono nominati responsabili, definiti tempi e indicatori chiave (KPI), e allocato un budget di massima. La pianificazione su una timeline condivisa garantisce trasparenza e controllo.
In questa fase, il change management si concentra sulla comunicazione visiva: dashboard interattive, poster operativi e bacheche digitali rendono trasparenti obiettivi, risultati e prossime azioni a tutti i livelli aziendali.
Coinvolgere le persone giuste, formarle sui nuovi processi e comunicare con chiarezza gli obiettivi permette di superare resistenze e assicurare un’adozione rapida. Senza una solida gestione delle risorse umane, anche i piani più brillanti rischiano di rimanere sulla carta.
Fase 4: esecuzione, monitoraggio e miglioramento continuo
L’implementazione avviene all’interno di cicli rapidi; ogni mese si raccolgono i dati di performance e si confrontano con la baseline iniziale. Il ciclo PDCA (Plan-Do-Check-Act) guida la riflessione sulle deviazioni, consentendo di correggere il tiro in tempo reale.
Il monitoraggio del cost variance, ovvero la differenza tra i costi effettivi sostenuti e quelli preventivati, diventa il fulcro dell’analisi: un confronto puntuale mese per mese evidenzia scostamenti dovuti a inefficienze operative o fluttuazioni dei prezzi delle materie prime, guidando interventi mirati per riallineare i processi agli obiettivi di redditività.
Inoltre, strumenti digitali come sistemi di manutenzione predittiva, sensori IoT e analytics avanzati permettono di anticipare problemi e dedurre insight di processo con velocità impensabile fino a pochi anni fa.
Casi di studio reali
Danieli, leader mondiale nel settore siderurgico, ha ridotto del 50% le rilavorazioni grazie a controlli in ingresso e formazione specifica per gli operatori: nel rapporto di sostenibilità 2023, l’azienda ha dichiarato che “questa iniziativa ha generato un risparmio di 3 milioni di euro e un aumento dell’efficienza del 7%”. Questo ha tradotto in un incremento del margine operativo del 4% nel semestre.
Barilla ha rinnovato il layout della propria linea di confezionamento pasta, eliminando colli di bottiglia e adottando tecniche di flow manufacturing. Il risultato è stato una diminuzione del 35% dei tempi di setup e del 20% degli scarti, con un miglioramento del margine lordo del 6%.
Pirelli ha portato l’OEE degli impianti di vulcanizzazione dal 75% al 90% in otto mesi, coniugando workshop Kaizen e manutenzione predittiva. Il risparmio sui costi operativi è stato del 5%, generando un aumento del margine del 3%.
Danaher, multinazionale nel medicale, ha coinvolto oltre duemila dipendenti in sessioni di root cause analysis. In un anno, l’azienda ha ridotto i costi indiretti del 12%, liberando risorse per nuovi investimenti in R&S.
Il cost deployment va oltre il controllo delle spese: è l’opportunità per ripensare la cultura aziendale, allineare strategia e operazioni e creare un vantaggio sostenibile. In un futuro in cui l’intelligenza artificiale si integrerà sempre più nei processi, come potrà il cost deployment evolvere per sfruttare al meglio l’analisi predittiva e l’automazione avanzata?
Applicando analisi rigorose, piani mirati e un monitoraggio costante, le imprese possono affrontare le sfide del mercato con margini più solidi e una base di innovazione continua.
Scopri come implementare il Cost Deployment per ridurre i costi produttivi e migliorare l’efficienza operativa:
https://crossnova.com/le-guide-operative/cost-deployment-guida-operativa/
Strategy Deployment: Per progettare e implementare in modo efficiente un percorso di Miglioramento Continuo
https://crossnova.com/le-guide-operative/strategy-deployment/
Ottimizzare i processi produttivi chimici con il Cost Deployment
https://crossnova.com/cost-deployment-processi-produttivi/