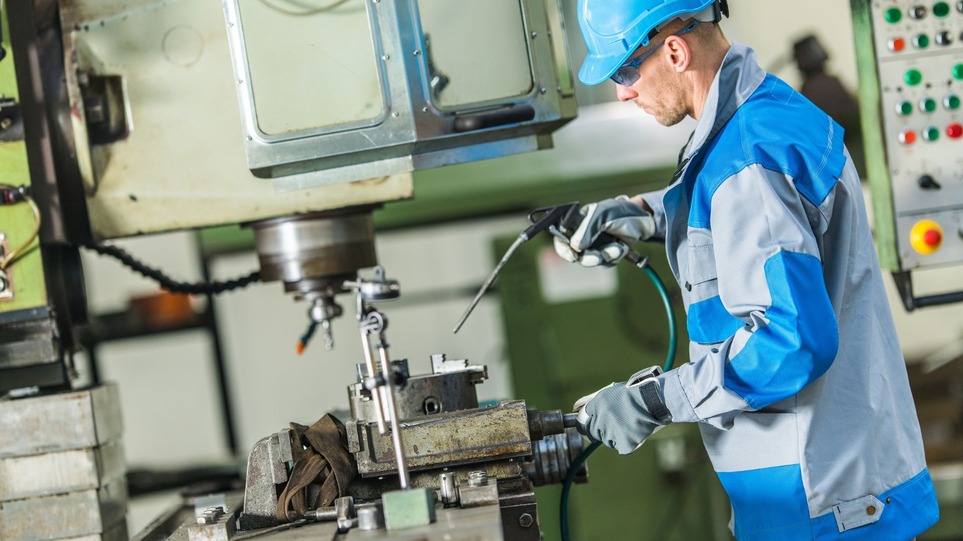
Riduzione dei tempi di gestione delle non conformità in un’azienda metalmeccanica
Nel settore metalmeccanico, con i suoi processi produttivi altamente complessi e una forte attenzione alla qualità, la gestione rapida delle non conformità è cruciale per garantire efficienza e soddisfazione del cliente. In questo articolo, esploriamo un caso di successo in cui una nota azienda metalmeccanica ha ottenuto una riduzione del 35% nei tempi di gestione delle non conformità di produzione, grazie all’applicazione di strumenti Lean e del ciclo PDCA. L’azienda in oggetto opera nel settore metalmeccanico, fornendo componenti personalizzati per l’industria automotive e mantenendo standard qualitativi elevati. Prima del progetto, il tempo medio di gestione delle non conformità era di oltre 15 giorni, causando ritardi di produzione e insoddisfazione del cliente. Una gestione più rapida delle non conformità è risultata quindi essenziale per migliorare il servizio e la competitività sul mercato.
Obiettivi del progetto
Il progetto aveva l’obiettivo di ridurre il tempo di gestione delle non conformità del 30% entro un anno, con l’intento di rispondere in modo più rapido ed efficace alle esigenze dei clienti e di diminuire i ritardi nel ciclo produttivo. Oltre a migliorare l’efficienza operativa, il progetto puntava anche ad elevare la qualità percepita dai clienti, incrementando la loro soddisfazione e fiducia nel prodotto.
- Per garantire risultati misurabili e sostenibili, è stata adottata la metodologia Lean, focalizzata sull’eliminazione degli sprechi e sull’ottimizzazione delle risorse
- A supporto di questa metodologia, è stato impiegato il ciclo PDCA (Plan-Do-Check-Act), un approccio iterativo che consente di monitorare e migliorare costantemente le prestazioni
Ogni fase del processo produttivo è stata attentamente analizzata per individuare potenziali inefficienze, con un particolare riguardo alle attività che non aggiungono valore. L’obiettivo finale era ottenere un sistema produttivo più snello e reattivo, capace di adattarsi rapidamente alle variazioni della domanda e di rispondere efficacemente alle esigenze del mercato, senza comprometterne la qualità.
Fase 1: analisi dello stato attuale
La prima fase ha coinvolto un’analisi dettagliata dei processi e l’identificazione dei principali colli di bottiglia. Attraverso il Value Stream Mapping (VSM), è stato possibile mappare le fasi di gestione delle non conformità, rilevando che il 40% dei ritardi si concentrava in due specifiche fasi del processo.
Strumenti utilizzati
- Value Stream Mapping (VSM): Visualizzazione delle fasi di gestione delle non conformità, identificando ritardi critici e tempi medi di attesa.
- 5 Why Analysis: Analisi delle cause profonde, che ha individuato le principali inefficienze operative e mancati allineamenti nei processi.
Fase 2: pianificazione delle azioni migliorative (Plan)
Dall’analisi è emerso un piano d’azione mirato, con l’introduzione di un monitoraggio in tempo reale e di una procedura standardizzata per la gestione delle non conformità. Il team ha definito priorità specifiche in base all’impatto, riducendo il tempo di gestione delle non conformità critiche del 50%.
Azioni implementate
- Dashboard di monitoraggio: Implementazione di un sistema di tracciamento in tempo reale per le non conformità, che ha ridotto il tempo di rilevamento iniziale del 20%.
- Standardizzazione delle procedure: Una procedura di gestione delle non conformità per garantire uniformità e rapidità, abbassando i tempi di risposta.
- Prioritizzazione delle non conformità: Definizione di un sistema di priorità basato su impatto e urgenza, per un intervento più efficiente sulle problematiche critiche.
Fase 3: implementazione (Do)
Le azioni pianificate sono state implementate gradualmente, con una formazione dedicata ai dipendenti per facilitare l’adozione delle nuove procedure. La formazione ha incrementato la competenza operativa, abbassando il tempo medio di risoluzione delle non conformità a 10 giorni, con un miglioramento del 33%.
Fase 4: monitoraggio e verifica (Check)
Dopo l’implementazione, il monitoraggio è avvenuto tramite KPI specifici, tra cui:
- Tempo medio di risoluzione delle non conformità: Ridotto da 15 a 10 giorni, per una diminuzione complessiva del 35%.
- Percentuale di non conformità risolte entro i termini: Passata dal 60% all’85%, riflettendo un’efficacia più elevata delle nuove procedure.
Fase 5: standardizzazione e Miglioramento Continuo (Act)
Grazie ai risultati ottenuti, le procedure sono state standardizzate e integrate nei processi aziendali. Il ciclo PDCA è ora una prassi consolidata per monitorare e migliorare continuamente la gestione delle non conformità, con la prospettiva di ulteriori ottimizzazioni.
Risultati raggiunti L’applicazione delle metodologie Lean e del ciclo PDCA ha portato a miglioramenti concreti:
- 35% di riduzione nei tempi di gestione delle non conformità, con un aumento della capacità produttiva.
- Aumento del 25% nella soddisfazione dei clienti grazie a tempi di risposta più rapidi.
- Miglioramento della qualità percepita e della capacità di rispondere proattivamente alle problematiche, consolidando la competitività aziendale.
Conclusioni
Questo caso di successo mostra l’efficacia degli strumenti Lean e del ciclo PDCA nel migliorare la gestione delle non conformità di produzione. La riduzione dei tempi di gestione ha portato a una maggiore efficienza interna e a una soddisfazione più alta dei clienti, dimostrando come un approccio strutturato possa trasformare i processi produttivi in un vantaggio competitivo.
Vuoi ottimizzare i processi della tua azienda e ridurre i tempi di gestione delle non conformità? Scopri subito come il team di Crossnova può supportarti con soluzioni Lean e PDCA personalizzate per le tue esigenze!