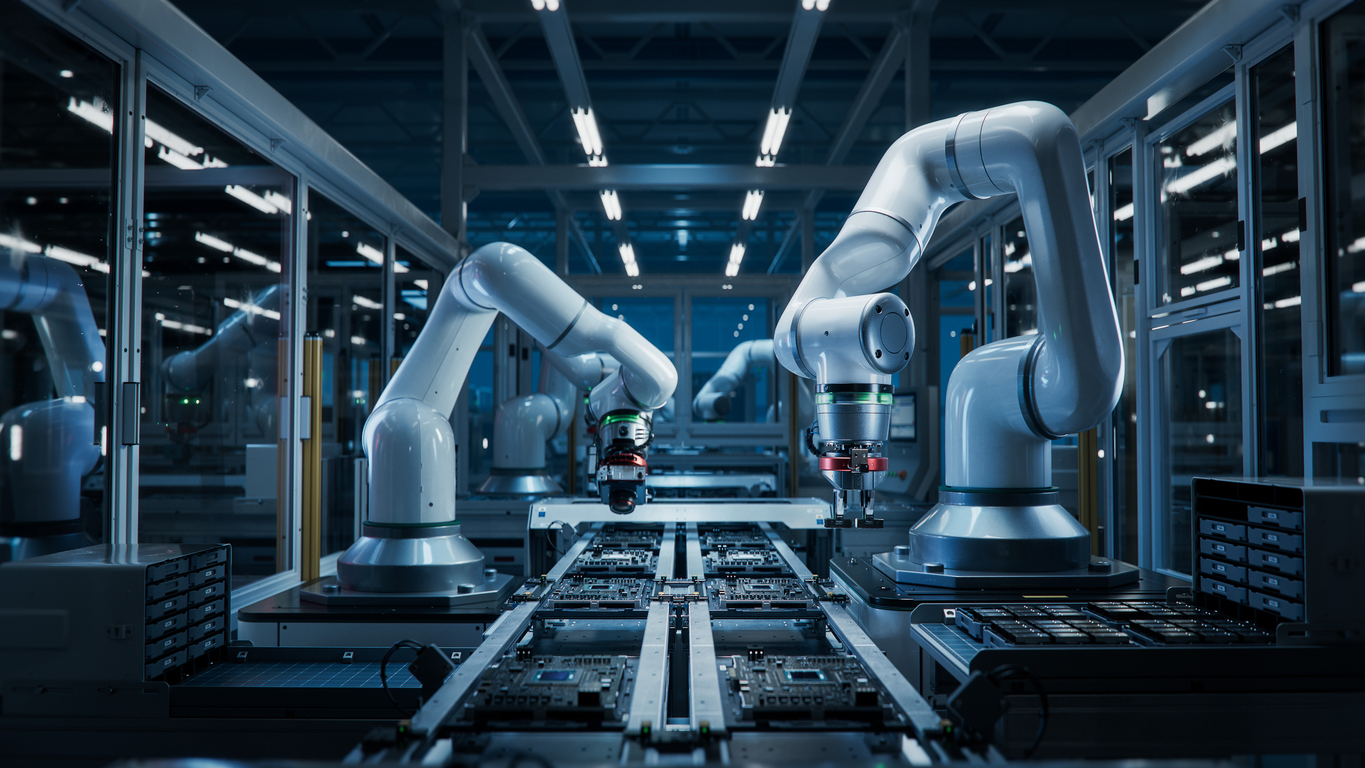
Total Productive Maintenance: ecco come migliora la tua produzione
In uno scenario produttivo in cui l’automazione, la robotica e l’IoT stanno riscrivendo le regole del gioco, la Total Productive Maintenance (TPM) si incorpora come uno dei pilastri per aggregare e controllare le nuove tecnologie, e da queste trarre tutto il vantaggio competitivo per cui sono state pensate.
Oggi, grazie all’innovazione, l’industria si affaccia verso un nuovo concetto di manutenzione, più puntuale e predittiva, in grado di ridurre i tempi di fermo macchina del 30-50% e aumentare il ciclo di vita delle apparecchiature del 20-40%, come conferma un’analisi di McKinsey.
In questo scenario high tech la TPM è una delle più efficaci metodologie di miglioramento del Lean Manufacturing che garantisce la disponibilità e l’affidabilità delle apparecchiature e delle linee di uno stabilimento attraverso alcune pratiche virtuose che incorporano concetti quali: prevenzione, zero difetti, zero incidenti e coinvolgimento degli operatori nelle attività di maintenance.
Cos’è la Total Productive Maintenance
La Total Productive Maintenance è dunque un approccio proattivo al tema della manutenzione dei macchinari. Secondo questa visione, dovrebbe essere delegato agli stessi operatori di produzione il compito di eseguire piccoli interventi di manutenzione sulle macchine direttamente presso le loro postazioni di lavoro. Il vantaggio collaterale di questa strategia è anche quello di lasciare ai tecnici di manutenzione più tempo per le attività core, ossia quelle che prevedono necessariamente la loro esperienza e le loro conoscenze settoriali.
L’obiettivo del TPM è massimizzare l’efficienza operativa di tutti, ridurre al minimo le perdite di produzione e migliorare la qualità dei prodotti azzerando gli sprechi legati alle apparecchiature, ossia i fermi macchina non programmati e i difetti di qualità dei prodotti.
Per controllare perdite di capacità e arresti delle linee, la manutenzione continua delle macchine gioca un ruolo strategico, diventando una parte integrante delle operations. Motivo per cui, tra i principi fondamentali della TPM, troviamo il coinvolgimento totale degli addetti alla produzione attraverso alcune buone pratiche quotidiane di semplice implementazione, come il controllo e i minimi interventi di riparazione e setup.
Gli 8 pilastri della TPM
La TPM non è sinonimo solo di manutenzione preventiva, è una disciplina molto più articolata che si fonda su 8 pilastri forgiati dal JIPM (Japan Institute of Plant Maintenance) grazie allo studio e alla dedizione di Seiichi Nakajima (1919-2015), ingegnere e insegnante giapponese. Le 8 pratiche che costituiscono l’ossatura della Total Productive Maintenance sono:
- Manutenzione autonoma: per rendere più Lean ed efficiente la produzione bisogna iniziare dal basso, incrementando poco a poco le migliorie. A questo scopo è necessario formare gli operatori in modo che possano occuparsi loro stessi delle piccole manutenzioni, siano queste preventive, ordinarie e in certi casi anche straordinarie. Come anticipato prima, questa strategia permette al personale di manutenzione più qualificato di riconvertire il proprio tempo in attività a più alto valore aggiunto, ovvero in riparazioni di elevato standard tecnico.
- Manutenzione preventiva: programmare attività di manutenzione preventiva permette di individuare con anticipo le cause di possibili anomalie che provocano interruzioni in produzione. Oggi è possibile tenere monitorato un alert che una macchina utensile lancia in produzione attraverso la sensoristica IoT e intervenire prima che sia troppo tardi.
- Miglioramento focalizzato: performare in modo efficiente significa adottare la logica operativa del ‘miglioramento continuo’. Per questo è cruciale scandagliare le cause più profonde di un’anomalia e intercettare i problemi giusti da risolvere. Nella complessità di uno scenario produttivo questo compito può risultare complicato, ma è di per sé una delle chiavi per ottenere il perfezionamento delle prestazioni. Occorre trovare il focus, la chiave per leggere il problema nel modo corretto e risolverlo con gli strumenti adeguati.
- Formazione e sviluppo delle competenze: il know-how organizzativo è uno degli asset più importanti da coltivare. La formazione sul campo degli operatori ha bisogno del sapere e del ‘saper fare’ per produrre i risultati sperati poiché le macchine, senza le competenze delle persone, non avranno modo di efficientare i processi in automatico. L’orientamento al miglioramento continuo delle attività di manutenzione diventa dunque una questione di cultura d’impresa.
- Sicurezza, salute e ambiente: per puntare all’efficienza occorre in primis creare un luogo di lavoro sicuro e pulito e un ambiente che non sia influenzato dalle attività umane. È necessario istituire un comitato che rappresenti tutti i dipendenti per definire e monitorare le azioni intraprese dall’azienda al fine di preservare queste condizioni.
- Gestione della qualità: questo pilastro della TPM si concentra sull’eliminazione sistematica delle non conformità che influiscono sulla qualità del prodotto. Occorre stabilire quali siano le condizioni dell’apparecchiatura che prevengono i difetti di qualità, basandosi sul concetto fondamentale di mantenere un’apparecchiatura perfetta coerente con gli standard qualitativi di produzione.
- Manutenzione pianificata: programmare attività di manutenzione pianificata significa in primis fare più efficienza grazie a macchine e attrezzature ben funzionanti e in grado quindi di ridurre al minimo le quantità di prodotti che si discostano dai desiderata del business.
- Gestione dei primi passi: tutte le conoscenze pratiche acquisite attraverso la TPM grazie a una comprensione più approfondita delle logiche di funzionamento delle macchine di produzione guiderà l’azienda verso la progettazione di nuove attrezzature ancor più efficienti.
I benefici della Total Productive Maintenance per la produzione
Una volta maturato nel tempo il proprio specifico know-how sulla base dei risultati ottenuti dalla TPM e dall’efficientamento dei processi di produzione, l’azienda è in grado di ridisegnare e progettare nuovi macchinari più performanti di prima. Queste attrezzature saranno più efficienti, conformi agli standard qualitativi ricercati, e soprattutto saranno costruite con l’obiettivo di evitare quanti più fermi macchina possibile.
Sviluppate sulla base delle conoscenze acquisite con la TPM, le nuove attrezzature devono essere disegnate per ridurre anche i periodi di inattività e i relativi costi di manutenzione. L’orientamento al Total Productive Maintenance ha come obiettivo finale di questo processo un miglioramento della qualità del prodotto.
Per ultimo, l’implementazione della TPM avrà come vantaggio un maggiore coinvolgimento e motivazione dei dipendenti, in quanto le attività di manutenzione eseguite dagli stessi operatori creano un legame più profondo tra il loro lavoro e la qualità del processo, generando un circolo virtuoso nella cultura organizzativa.
Conclusioni
La TPM dunque ha un grande potenziale di cambiamento nel know-how aziendale e nel funzionamento stesso delle operations. Per questo è fondamentale che i dipendenti comprendano fino in fondo i suoi obiettivi, affinché l’intervento di change management abbia un impatto profondo sul miglioramento continuo. Implementare questa strategia, soprattutto se affiancati da un esperto, significa iniziare un percorso di trasformazione che offre vantaggi competitivi anche nell’innovazione di prodotto, dei macchinari e, perché no, di processo.
Scopri subito come applicare questi principi in azienda!