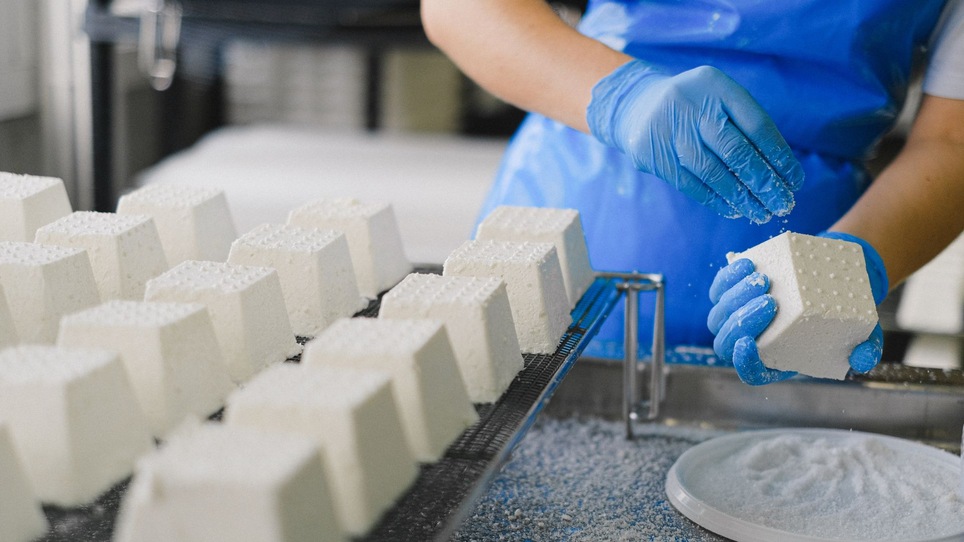
Stabilità, qualità e risparmio: come un progetto di controllo di processo ha salvato 143.000 Euro
Negli ultimi semestri, un’importante azienda italiana del settore lattiero-caseario si è trovata ad affrontare una sfida produttiva di rilievo, che ha messo in seria difficoltà la tenuta dell’intero sistema operativo.
In particolare, si è registrato un aumento significativo del numero di pezzi difettosi e un conseguente incremento delle rilavorazioni, due sintomi evidenti di una produzione che aveva perso stabilità e controllo.
Questa situazione ha generato una doppia criticità. Da un lato, la crescente non conformità dei prodotti ha comportato un forte impatto economico, con una stima di perdite che ha toccato i 110.000 Euro in un solo semestre — un valore che includeva sia il costo diretto dei pezzi distrutti che quello indiretto legato a rilavorazioni, fermi macchina e spreco di risorse. Dall’altro lato, l’imprevedibilità del processo ha causato instabilità nella pianificazione produttiva, con riflessi importanti anche sulla gestione dello stock di magazzino, spesso messo sotto pressione dalla necessità di compensare con scorte di sicurezza.
Il sistema, privo di strumenti adeguati di controllo di processo e standardizzazione, diventava sempre più dipendente dalla soggettività degli operatori, rendendo difficile garantire la qualità in modo coerente e ripetibile. Il rischio non era solo di tipo produttivo, ma strategico: compromettere la fiducia dei clienti e perdere competitività in un mercato dove la qualità del prodotto e la puntualità della consegna sono fattori chiave per il successo.
Un approccio strutturato grazie al Lean Six Sigma
Per affrontare in modo strutturato ed efficace le criticità emerse, l’azienda ha deciso di avviare un progetto strategico di controllo di processo, facendo leva sulle metodologie Lean Six Sigma, riconosciute a livello internazionale per la loro efficacia nel migliorare le performance dei processi produttivi e ridurre la variabilità.
L’obiettivo era ambizioso ma chiaro:
- Ridurre la variabilità di processo, rendendo la produzione più prevedibile e standardizzata;
- Migliorare la qualità del prodotto, agendo sulle cause profonde delle non conformità;
- Eliminare gli sprechi, in particolare quelli legati a rilavorazioni, scarti e tempi improduttivi.
Il cuore metodologico dell’intervento è stato l’utilizzo del ciclo DMAIC (Define, Measure, Analyze, Improve, Control), una delle colonne portanti del Lean Six Sigma. Questo approccio ha permesso di affrontare il problema non in modo reattivo, ma basandosi su dati oggettivi e analisi rigorose:
- Nella fase di Define, sono stati chiaramente definiti obiettivi, ambito del progetto e indicatori di prestazione (KPI), coinvolgendo tutte le funzioni aziendali interessate;
- Con la fase di Measure, è stata avviata una raccolta sistematica dei dati relativi alla difettosità e alle rilavorazioni, permettendo di fotografare con precisione lo stato attuale del processo;
- Nella fase di Analyze, il team ha indagato le cause profonde (root causes) delle non conformità, utilizzando strumenti analitici e statistici per identificare con precisione le variabili critiche che influenzavano la qualità;
- La fase di Improve ha portato all’implementazione di soluzioni concrete: modifiche ai parametri di processo, aggiornamenti delle procedure operative standard (SOP), formazione mirata al personale e introduzione di nuovi strumenti di controllo qualità;
- Infine, con la fase di Control, sono stati messi in atto meccanismi di monitoraggio e controllo continuo, per assicurare la sostenibilità nel tempo dei miglioramenti ottenuti e prevenire ricadute.
Grazie a questo approccio, l’azienda ha potuto trasformare una criticità in un’opportunità di crescita, ottenendo benefici misurabili e diffondendo una nuova cultura del miglioramento continuo.
Risultati concreti: stabilità e risparmio
Il progetto di Controllo di Processo ha portato a risultati concreti e misurabili. Un’ulteriore conferma di quanto un approccio strutturato e data-driven possa migliorare efficienza operativa e redditività.
Attraverso un’analisi puntuale dei dati e azioni correttive mirate, si è ottenuta una riduzione del tasso di difettosità del 7%. Questo miglioramento ha inciso positivamente sulla qualità del prodotto e sulla percezione da parte del cliente finale.
In parallelo, le rilavorazioni sono diminuite dell’8%, con un doppio vantaggio: meno sprechi di tempo e risorse, maggiore fluidità del processo produttivo.
Tra i risultati più significativi c’è la riduzione del 10% dei costi operativi legati ai controlli qualità e al campionamento.
L’introduzione di strumenti più efficienti e di un monitoraggio proattivo ha reso il processo di verifica più snello ed efficace.
Le risorse sono state utilizzate meglio, con un impatto diretto sull’ottimizzazione dei costi.
Il progetto ha previsto anche l’internalizzazione di alcune attività di manutenzione precedentemente esternalizzate. Questo ha generato un risparmio diretto stimato in 8.000 euro all’anno.
In più, ha favorito lo sviluppo di nuove competenze interne, rafforzando il know-how del team e migliorando la capacità di risposta in tempo reale.
Nel complesso, l’iniziativa ha prodotto un saving annuo di 143.000 euro.
Un risultato che dimostra come l’adozione di logiche Lean Six Sigma e una gestione partecipativa del cambiamento possano generare benefici reali, sia economici che organizzativi e culturali.
Il valore delle persone e dei dati
Oltre ai risultati economici e operativi, il progetto ha generato un impatto significativo anche sul piano culturale e organizzativo. È diventato un vero catalizzatore di cambiamento interno.
Una delle leve principali è stata la promozione di una cultura orientata al dato. La raccolta, l’analisi e l’interpretazione delle informazioni sono diventate strumenti quotidiani a supporto delle decisioni.
L’iniziativa ha stimolato una nuova consapevolezza all’interno dei team. Comprendere il valore strategico dei dati ha permesso di superare approcci soggettivi e reattivi. Si è così favorita una gestione più oggettiva, misurabile e orientata al miglioramento continuo.
Per rendere possibile questo cambiamento, è stata avviata una riorganizzazione di ruoli e competenze. L’obiettivo era dare maggiore chiarezza alle responsabilità, valorizzare il contributo di ciascuno e creare un clima di coinvolgimento diffuso.
I collaboratori sono stati coinvolti fin dalle prime fasi. Non sono stati semplici esecutori, ma veri protagonisti del cambiamento. Questo ha aumentato motivazione e senso di appartenenza, elementi chiave per la sostenibilità dei risultati nel tempo.
Uno degli snodi centrali del percorso è stato l’introduzione di un sistema di controllo di processo proattivo. Questo approccio ha rappresentato una vera svolta rispetto al passato, rafforzando ulteriormente il concetto di controllo di processo come leva strategica per garantire qualità e affidabilità. Non si è più lavorato solo sull’ispezione del risultato finale, ma su un modello capace di intercettare le deviazioni prima che causassero problemi.
Il team Crossnova ha avuto un ruolo determinante, affiancando l’azienda con un supporto costante, sia metodologico che operativo. Dalla diagnosi iniziale alla definizione degli obiettivi, dalla formazione alla gestione del cambiamento, ha messo in campo competenze analitiche, tecniche e gestionali rivelatesi decisive per il successo del progetto.
Il vero valore aggiunto è stato l’approccio: collaborativo, concreto e orientato al risultato. Le soluzioni sono state adattate alle specificità del contesto produttivo e culturale dell’azienda.
📌 Hai l’obiettivo di migliorare l’efficienza e ridurre gli sprechi nella tua azienda?
Scopri come trasformare le criticità produttive in vantaggi competitivi!