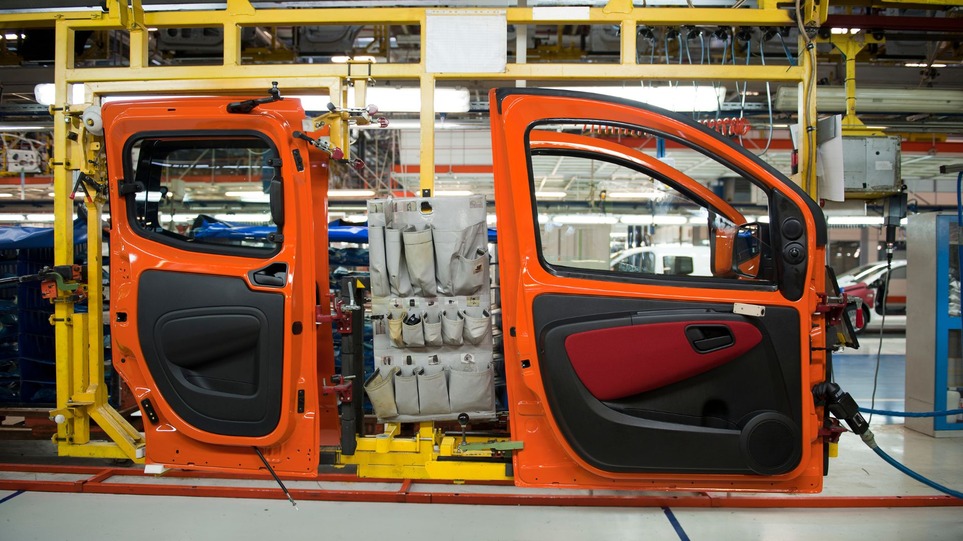
Riduzione dei costi del lubrorefrigerante: un progetto di Focused Improvement nel settore automotive
Nel settore automotive, la competizione è feroce e ogni euro risparmiato può fare la differenza tra marginalità e perdita. In quest’ottica, un’azienda leader nella produzione di veicoli con un fatturato annuo di 100 milioni di euro e 290 dipendenti ha intrapreso un progetto di Focused Improvement per ridurre i costi associati al consumo di olio lubrorefrigerante.
L’obiettivo principale era abbattere i costi del lubrorefrigerante, una delle voci di spesa più consistenti nella gestione delle macchine utensili dell’azienda, mantenendo però alti gli standard di qualità e produttività.
Il costo iniziale annuale del lubrorefrigerante era di circa 250.000 euro, una cifra significativa che rappresentava un’opportunità per un intervento mirato di miglioramento continuo.
La metodologia: come è stato condotto il progetto
Il progetto ha seguito i principi del Focused Improvement, parte integrante della filosofia Lean Manufacturing e del Total Productive Maintenance (TPM). Questo approccio prevede un’analisi sistematica delle inefficienze per individuare e implementare soluzioni sostenibili.
Identificazione del Team di progetto
Guidati dal supporto del team Crossnova, per il successo del progetto di riduzione dei costi del lubrorefrigerante, è stato essenziale formare un team multidisciplinare che integrasse competenze complementari e una visione olistica dei processi aziendali. Questo approccio ha permesso di affrontare il problema da diverse prospettive, garantendo soluzioni pratiche e sostenibili.
- Gli operatori delle macchine utensili hanno fornito una conoscenza diretta e dettagliata delle sfide operative quotidiane, come il dosaggio del lubrorefrigerante e la gestione delle sostituzioni. La loro esperienza pratica ha contribuito a identificare i punti critici e le inefficienze nei processi
- I manutentori esperti hanno messo a disposizione competenze tecniche fondamentali per analizzare i sistemi di lubrificazione e proporre miglioramenti strutturali, come l’adozione di filtri avanzati e la manutenzione preventiva
- I tecnici del controllo qualità hanno garantito che ogni intervento non compromettesse gli standard elevati richiesti dal settore automotive, contribuendo a definire le specifiche dei lubrorefrigeranti e monitorando eventuali impatti sui prodotti finiti
- Infine, i responsabili di produzione e acquisti hanno fornito una visione strategica. Hanno valutato i costi complessivi, negoziato con i fornitori per ottenere materiali più performanti e supportato l’implementazione delle soluzioni con un approccio sistemico
Questa collaborazione interdisciplinare è stata cruciale per sviluppare un piano d’azione efficace, capace di coniugare efficienza operativa e risparmi economici.
Analisi del problema
Attraverso una combinazione di strumenti come SIPOC Diagram, Value Stream Mapping, analisi temporali e Diagramma di Pareto, il team ha individuato le principali cause di spreco:
- Eccessivo consumo del lubrorefrigerante dovuto a scarse regolazioni nei dosaggi.
- Perdite durante i cambi a causa di sistemi di drenaggio inefficienti.
- Frequenti sostituzioni dovute a contaminazioni.
Sperimentazione e implementazione delle soluzioni
Dopo un’analisi approfondita delle inefficienze nel consumo del lubrorefrigerante, il team ha implementato un insieme di soluzioni mirate che hanno portato a risultati concreti. Uno dei primi interventi è stato l’ottimizzazione del dosaggio automatico del lubrorefrigerante, realizzata grazie all’installazione di sensori di ultima generazione. Questi dispositivi hanno permesso un controllo più preciso, evitando sprechi e garantendo che ogni macchina ricevesse esattamente la quantità necessaria di fluido.
Un’altra misura chiave è stata l’introduzione di un sistema di filtraggio avanzato, che ha significativamente aumentato la vita utile del lubrorefrigerante. Questo sistema ha ridotto la frequenza delle sostituzioni, generando risparmi sia sui materiali che sulle ore di lavoro dedicate alla manutenzione.
Per garantire che le soluzioni implementate fossero sostenibili nel lungo termine, è stata organizzata una formazione specifica per gli operatori, concentrata sulle migliori pratiche per la gestione dei fluidi. Gli operatori hanno acquisito competenze per monitorare i livelli e la qualità del lubrorefrigerante, minimizzando i rischi di errori.
Infine, sono state riviste e migliorate le procedure di manutenzione, con un focus particolare sulla prevenzione delle contaminazioni. Questo ha incluso l’adozione di protocolli più rigorosi per la pulizia delle attrezzature e la sostituzione dei componenti critici.
Questi interventi, combinati, hanno non solo ridotto i costi ma anche migliorato l’efficienza operativa e la sostenibilità dell’intero processo produttivo.
Monitoraggio e valutazione
Grazie all’implementazione di KPI specifici, come il consumo mensile di lubrorefrigerante e il costo per macchina, il team ha monitorato i progressi e apportato ulteriori miglioramenti dove necessario.
I risultati: numeri concreti
Dopo 12 mesi di lavoro, i risultati sono stati sorprendenti:
- Riduzione dei costi annuali del 38%, pari a un risparmio di circa 95.000 euro.
- Diminuzione del consumo di lubrorefrigerante del 40%.
- Aumento della vita utile del lubrorefrigerante del 50%, grazie al miglior filtraggio.
- Riduzione del downtime delle macchine legato alla gestione del lubrorefrigerante del 15%.
Questi risultati non solo hanno migliorato la redditività dell’azienda, ma hanno anche avuto un impatto positivo sull’ambiente, riducendo la quantità di rifiuti speciali prodotti.
Un’opportunità di miglioramento
Il progetto di Focused Improvement ha dimostrato come un approccio strutturato e collaborativo possa portare a risultati concreti e sostenibili. L’azienda, grazie al successo ottenuto, ha deciso di estendere l’applicazione della metodologia ad altre aree, consolidando il proprio impegno verso l’innovazione e l’efficienza. In un settore competitivo come l’automotive, ottimizzare i processi interni è fondamentale. Questo caso dimostra che anche una voce di costo apparentemente “ordinaria” può diventare un’opportunità di miglioramento strategico.
📌 Vuoi anche tu ridurre i costi e migliorare l’efficienza produttiva?
Scopri come applicare il Focused Improvement nella tua azienda!