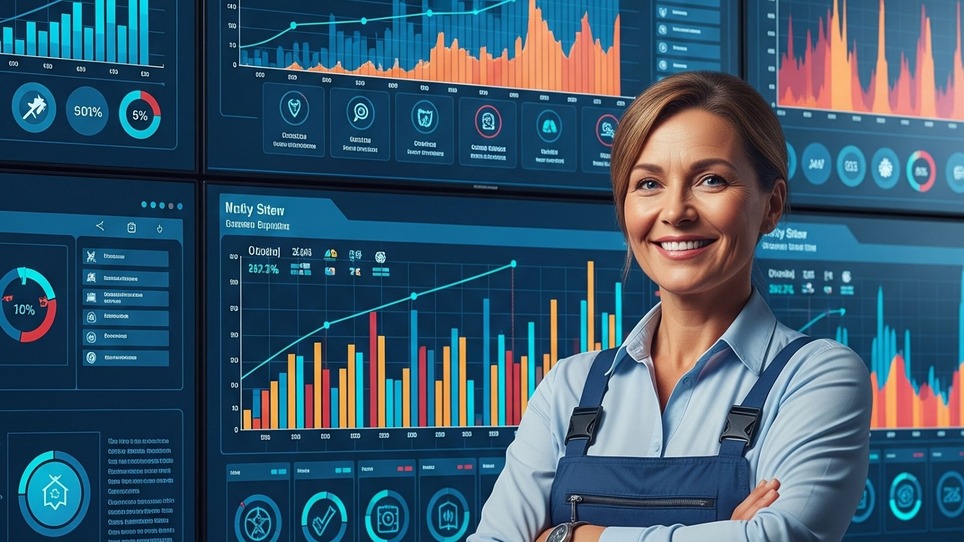
Ottimizzazione della performance nei loops di regolazione: l’approccio Lean Six Sigma con Crossnova
La regolazione dei processi produttivi è un elemento chiave per garantire la qualità e l’efficienza operativa. Questo è stato il focus del progetto intrapreso presso un importante impianto industriale, dove il supporto di Crossnova ha consentito di migliorare le performance dei “loops di regolazione”, elementi cruciali per la gestione degli input di processo. Attraverso il metodo Lean Six Sigma, il team ha implementato soluzioni mirate, ottenendo risultati significativi in termini di riduzione della variabilità e ottimizzazione dei processi.
Obiettivi e sfide del progetto
La sfida iniziale era garantire che gli input di processo chiave (portate di aria, olio, metano e inibitori) si mantenessero entro fasce di controllo definite, riducendo la deviazione dal setpoint (%DSP). Ogni scostamento rappresentava un difetto, con impatti negativi sulla qualità del prodotto e sull’efficienza complessiva. Il progetto mirava a migliorare la capability dei processi, misurata tramite indici Cp e CpK, per raggiungere un controllo più stabile e preciso.
Implementazione del ciclo DMAIC
Define
Nella fase Define, il team ha identificato con precisione le metriche critiche di qualità (CTQ) necessarie per monitorare e migliorare la performance dei loops di regolazione. L’indicatore primario scelto è stato la %DSP (Percentuale di Deviazione dal Setpoint), una misura chiave per valutare quanto i valori di processo reali si discostassero dai target prefissati. Per ogni loop di regolazione sono state definite fasce di controllo specifiche, delineando i limiti entro cui la deviazione sarebbe stata considerata accettabile. Parallelamente, è stato elaborato un business case che ha evidenziato l’importanza strategica del progetto, sottolineando come la riduzione della variabilità negli input di processo fosse essenziale per garantire una qualità costante del prodotto finale. Questa chiarezza obiettiva ha fornito una base solida per indirizzare le fasi successive verso soluzioni mirate ed efficaci.
Measure
Nella fase Measure, il team ha condotto una raccolta dati sistematica per ottenere una panoramica dettagliata delle performance dei loops di regolazione. I dati sono stati registrati automaticamente ogni 20 minuti per un periodo di due settimane, utilizzando un sistema avanzato interfacciato con i sensori di processo. Questa metodologia ha consentito di raccogliere informazioni precise e puntuali su ogni loop, incluse le deviazioni rispetto ai setpoint. L’analisi preliminare ha evidenziato criticità rilevanti: alcune deviazioni significative indicavano una gestione non ottimale, mentre gli indici di capability (CpK) si sono rivelati inferiori a 1,00 per diversi loops, segnalando un livello di controllo inadeguato. I rendimenti variavano considerevolmente, oscillando tra il 78,9% e il 98,4%, mettendo in luce ampi margini di miglioramento per stabilizzare e ottimizzare i processi.
Analyze
Nella fase Analyze, il team ha indagato a fondo le cause della variabilità nei loops di regolazione utilizzando strumenti analitici avanzati. Il diagramma di Ishikawa ha permesso di mappare le potenziali cause ed effetti, mentre l’analisi di capability ha fornito un quadro quantitativo delle prestazioni dei processi rispetto agli obiettivi prefissati. È emerso che i parametri PID, fondamentali per il controllo dei loops, erano non ottimali, contribuendo a deviazioni significative dal setpoint. Inoltre, la tecnologia di controllo utilizzata si è rivelata obsoleta, incapace di garantire un’efficienza operativa adeguata. Un’ulteriore criticità era rappresentata dall’assenza di standardizzazione nelle operazioni manuali, che introduceva ulteriori variazioni nei processi. Questi risultati hanno offerto una chiara direzione per gli interventi di miglioramento nelle fasi successive.
Improve
Nella fase Improve, il team ha implementato interventi mirati per affrontare le cause principali della variabilità nei loops di regolazione. Una delle azioni principali è stata l’ottimizzazione dei parametri PID, con l’obiettivo di ridurre la variabilità e migliorare la stabilità del sistema. Parallelamente, è stato aggiornato il sistema di controllo, sostituendo la tecnologia obsoleta con soluzioni più moderne e precise, capaci di rispondere meglio alle esigenze operative. Per garantire uniformità, si è proceduto alla standardizzazione delle operazioni, introducendo registri per monitorare e distinguere chiaramente tra modalità manuale e automatica. Inoltre, per alcuni loops specifici, è stata valutata la sostituzione degli elementi finali di controllo sovradimensionati, che non rispettavano le best practices ingegneristiche, al fine di migliorare ulteriormente le performance del processo. Questi interventi hanno posto le basi per un controllo più efficace e una maggiore affidabilità complessiva del sistema.
Control
Nella fase Control, il team ha monitorato attentamente le performance dei loops di regolazione per verificare la sostenibilità degli interventi implementati. I dati raccolti hanno evidenziato progressi significativi: la deviazione %DSP è stata ridotta rispetto ai livelli iniziali, indicando un maggiore controllo sui processi. Il rendimento operativo è aumentato, raggiungendo il 91,85% per il loop dell’aria e l’86,34% per quello dell’inibitore, segnando un netto miglioramento rispetto alle performance precedenti. Anche gli indici di capability (CpK) hanno mostrato un avanzamento, benché siano rimasti al di sotto della soglia critica di 1,00. Questo suggerisce che, nonostante i risultati positivi, esistono ulteriori margini di miglioramento per ottimizzare completamente la capacità di controllo del sistema. Questi risultati forniscono una base solida per interventi futuri e assicurano un controllo continuo dei processi.
Risultati e impatti
Il progetto ha dimostrato come l’approccio Lean Six Sigma possa essere un potente strumento per affrontare problemi complessi e migliorare le performance operative. Il supporto di Crossnova è stato cruciale nell’analisi e nell’implementazione delle soluzioni, garantendo risultati misurabili e sostenibili. Questo progetto non solo ha migliorato i loops di regolazione coinvolti, ma ha creato una base solida per estendere queste best practices ad altri processi produttivi, con un impatto diretto su qualità e costi operativi.
📌 Vuoi migliorare il controllo dei tuoi processi produttivi?
Con Crossnova trasformi i tuoi loops di regolazione in un vantaggio competitivo.