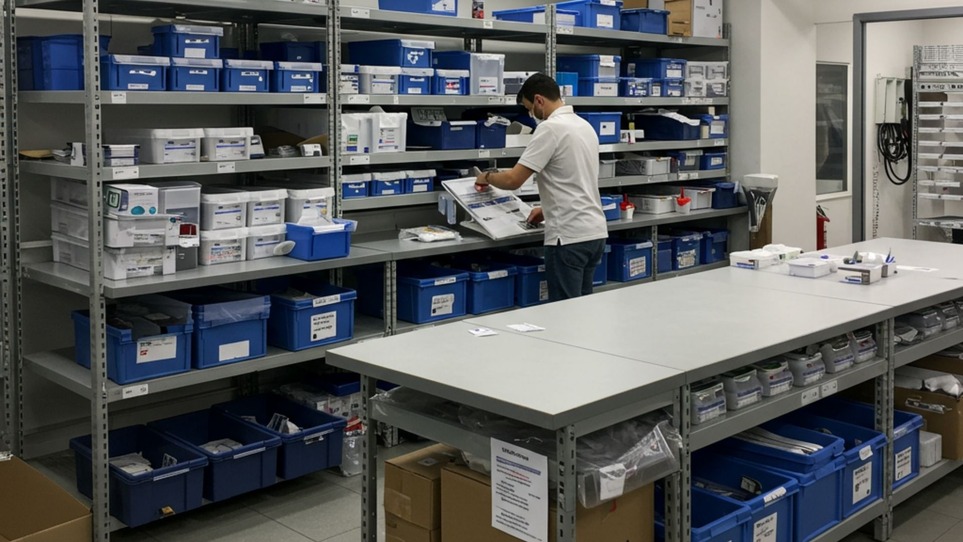
Ottimizzazione dei rifornimenti nell’area premontaggi: come migliorare l’efficienza nei processi industriali
Le aziende impegnate nella progettazione e produzione di impianti e apparecchiature industriali stanno acquisendo una consapevolezza sempre più profonda: per restare competitive in un mercato dinamico e ad alta pressione, è essenziale saper coniugare velocità produttiva, flessibilità operativa e controllo dei costi. In questo scenario, l’efficienza operativa non è più un’opzione, ma una vera e propria priorità strategica, capace di fare la differenza tra una struttura produttiva reattiva e una che fatica a sostenere le richieste del mercato.
- Tra i principali fattori che incidono su tale efficienza, la gestione dei materiali assume un ruolo determinante.
- Disporre di un sistema ben organizzato per il rifornimento e la distribuzione dei componenti, in particolare nelle aree di premontaggio, consente di evitare interruzioni nel flusso produttivo, ridurre i tempi di attesa e minimizzare gli sprechi legati a stock inutilizzati o approvvigionamenti non coordinati.
L’ottimizzazione del rifornimento dei materiali nell’area premontaggi rappresenta quindi una leva fondamentale per migliorare le performance produttive. Intervenire su questo specifico ambito significa agire direttamente sulla continuità e sulla qualità del processo di assemblaggio, con benefici tangibili in termini di produttività, ordine, sicurezza e utilizzo efficiente degli spazi.
Tali risultati non si raggiungono per tentativi, ma richiedono l’applicazione di metodologie strutturate, come l’analisi dei flussi logistici, la razionalizzazione delle scorte, la standardizzazione delle operazioni e l’introduzione di strumenti lean come le 5S. Fondamentale in questo percorso è anche l’impiego di partner specializzati, in grado di supportare l’azienda nella caratterizzazione dei processi esistenti, nell’individuazione delle criticità e nello sviluppo di soluzioni su misura, come ha dimostrato l’esperienza condotta con Crossnova.
Le sfide nella gestione dei materiali in area premontaggi
La gestione della minuteria e dei componenti di piccole dimensioni avviene ancora attraverso modalità di tipo “self service”. In questo modello, gli operatori di linea si recano direttamente in un’area di stoccaggio interna, spesso denominata “supermarket”, per prelevare in autonomia il materiale necessario. Sebbene questa prassi sia ampiamente diffusa per la sua apparente semplicità organizzativa, abbiamo rilevato che presenta numerose criticità che impattano negativamente sull’efficienza complessiva del reparto.
- Una delle problematiche più ricorrenti è la frequente condizione di sotto scorta: la mancanza di un sistema strutturato di controllo dei livelli minimi comporta che i materiali non siano sempre disponibili al momento del bisogno. Ciò genera ritardi nel flusso produttivo, interruzioni nei cicli di lavoro e, in alcuni casi, veri e propri fermi linea, con evidenti ricadute su tempi e costi.
- In parallelo, l’approvvigionamento diretto da parte degli operatori porta spesso a un’occupazione eccessiva degli spazi operativi. I banchi di lavoro si riempiono di contenitori di minuteria, molti dei quali contengono codici ridondanti o non più necessari. Questo genera disordine, ostacola l’ergonomia delle postazioni e aumenta i tempi di ricerca del materiale corretto.
- Infine, l’intero processo risente di una mancanza di flussi definiti: non esistono percorsi chiari e tracciabili per l’ingresso e l’uscita del materiale, né una gestione visuale che consenta di comprendere a colpo d’occhio lo stato delle scorte. Questo disordine logistico non solo riduce la produttività, ma rende anche più complessa l’identificazione di anomalie, dispersioni o errori di prelievo.
Un progetto di efficientamento: dalla mappatura al controllo
Per affrontare in modo strutturato le criticità rilevate nella gestione della minuteria, è stato avviato un progetto di miglioramento continuo articolato secondo la metodologia DMAIC (Define, Measure, Analyze, Improve, Control).
Il punto di partenza è stato un approfondito lavoro di analisi dei processi esistenti (“as is”), che ha evidenziato le inefficienze operative legate alla disponibilità dei materiali, alla saturazione degli spazi e alla mancanza di standard visivi.
Nel corso della fase “Define”, è stata identificata un’area pilota all’interno del reparto “montaggio sottogruppi”, selezionata per la sua rappresentatività e per la possibilità di implementare rapidamente azioni di miglioramento. In questa area, ad esempio, si registrava una media settimanale di 5–6 casi in cui i materiali risultavano assenti dal supermarket, con conseguenti rallentamenti nel processo produttivo. Inoltre, è emersa la presenza di fino a 15 codici di minuteria non necessari in ciascun banco di lavoro, che occupavano spazio prezioso e creavano confusione.
Attraverso l’applicazione del metodo 5S, è stata avviata un’azione mirata di semplificazione, riordino e standardizzazione. Il primo step ha previsto un audit approfondito volto a identificare il materiale superfluo, con una riduzione immediata degli articoli presenti sulle postazioni del 30%. Contestualmente, è stata migliorata la tracciabilità del materiale grazie a una nuova disposizione codificata dei contenitori e alla creazione di zone di ingresso/uscita chiaramente definite per il materiale assemblato e da assemblare.
Il supporto di Crossnova
La collaborazione con Crossnova, specializzata nella caratterizzazione e ottimizzazione dei processi industriali, ha giocato un ruolo chiave nel progetto. Con il supporto del team Crossnova è stato possibile raccogliere dati oggettivi e misurabili – come il tempo medio dedicato dagli operatori al reperimento della minuteria (ridotto da oltre 20 minuti al giorno a meno di 8 minuti) – e sviluppare soluzioni su misura allineate con le esigenze del reparto.
L’efficacia delle azioni è stata monitorata attraverso specifici KPI (Key Performance Indicators), tra cui:
- Riduzione del numero medio di sotto scorte settimanali al supermarket, passato da 18 a 5 casi.
- Diminuzione del tempo medio di rifornimento dal magazzino centrale di oltre il 50%.
- Recupero di circa 4 m² di spazio utile per ogni postazione, grazie alla rimozione dei contenitori ridondanti.
Questi risultati, ottenuti in tempi brevi e con risorse mirate, hanno dimostrato l’efficacia dell’approccio strutturato e hanno posto le basi per l’estensione del modello ad altri reparti produttivi.
I vantaggi: maggiore ordine, meno attese, più sicurezza
L’approccio sistematico ha portato a risultati tangibili:
- Riduzione drastica dei tempi di attesa per il reperimento della minuteria.
- Ordine e pulizia migliorati nei banchi di lavoro, con conseguente aumento della produttività.
- Ottimizzazione del flusso dei materiali dal magazzino centrale all’area di utilizzo.
- Valutazione ergonomica delle postazioni, con benefici sulla salute e sicurezza degli operatori.
Standardizzazione e prospettive future
Il progetto non si è fermato alla sperimentazione: le soluzioni implementate sono state standardizzate tramite OPL (One Point Lessons) e il confronto tra la situazione iniziale e quella finale ha evidenziato miglioramenti consistenti. Le fasi successive prevedono l’estensione del modello ad altre aree produttive, sempre con il supporto metodologico di Crossnova.
Conclusione
L’efficienza nei processi di rifornimento in ambito industriale non è solo una questione logistica: è una componente essenziale della competitività aziendale. Interventi mirati, basati su dati e su metodi strutturati, possono trasformare criticità operative in opportunità di miglioramento continuo.
📌 Vuoi ridurre attese, sotto scorte e sprechi nella tua area di premontaggio?
Affidati a Crossnova e rendi il rifornimento un punto di forza produttivo.