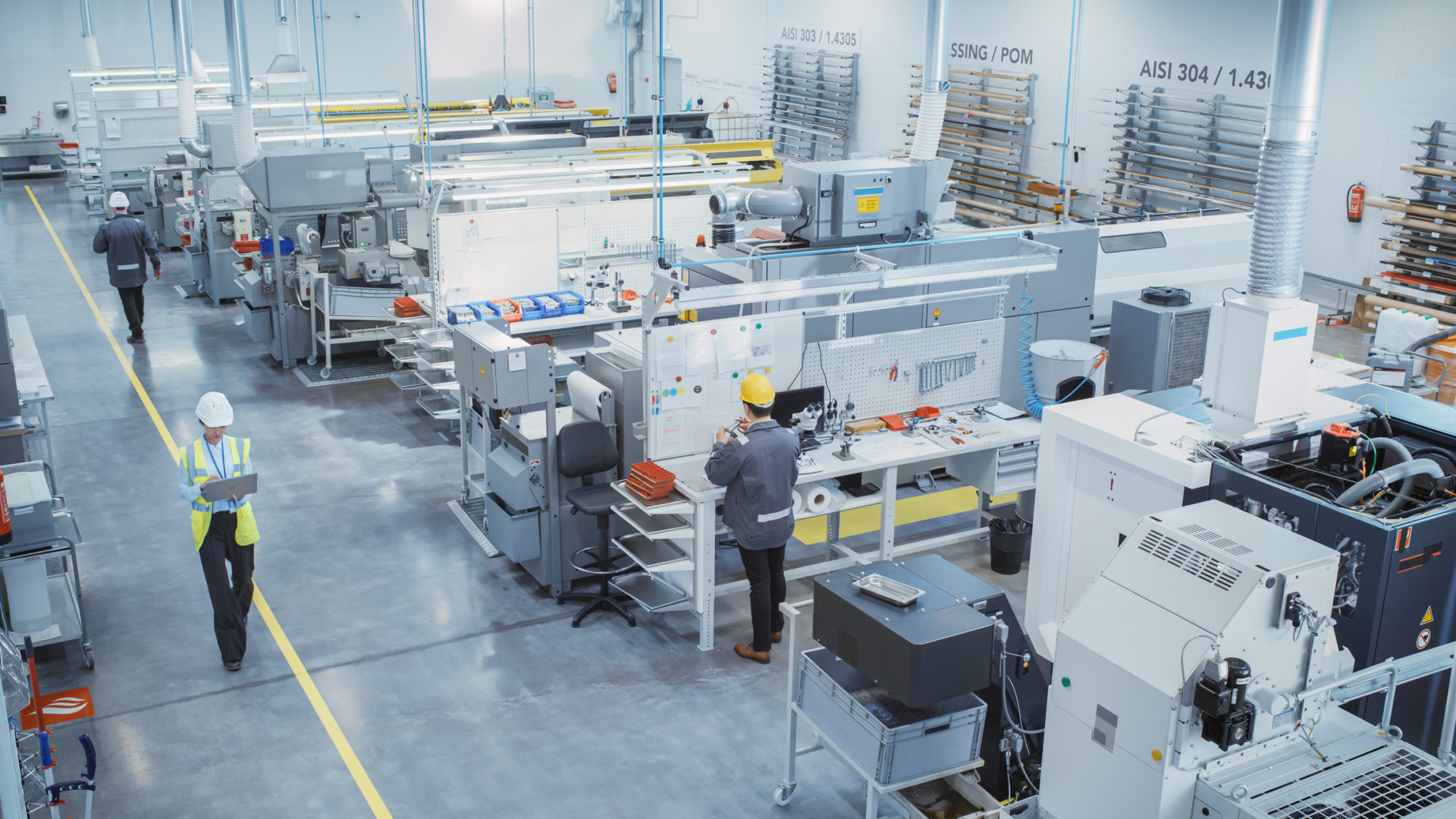
Efficienza produttiva: ecco i KPI da tracciare
Sempre più le organizzazioni sono chiamate oggi a concentrarsi sulla loro capacità produttiva e sul loro livello competitivo. Queste due sfide ingombranti costringono le imprese a utilizzare le proprie risorse in modo strategico per trarne il massimo vantaggio. In che modo è possibile ottimizzare tutto ciò che già è a disposizione? Una strada percorribile è attraverso il perfezionamento dell’efficienza produttiva.
Essere efficienti in produzione determina a sua volta la quota più o meno grande di prodotto su cui l’azienda avrà modo di marginalizzare a parità di tempo e risorse impiegate. Motivo per cui ambire a un processo di miglioramento continuo risulta un fattore competitivo cruciale. Per centrare questo obiettivo ogni azienda deve saper bilanciare con cura la relazione tra i prodotti, i beni o i servizi e le risorse disponibili, combinando così l’efficacia con l’efficienza nella misura della sua performance organizzativa.
Che cos’è l’Overall Equipment Effectiveness (OEE)
Raggiungere un’efficienza produttiva capace di accelerare la crescita significa riuscire a trarre ogni beneficio dalla quantità di risorse disponibili, il che equivale a una sola cosa: minimo spreco e massima resa. Per ottenerla occorre in primis calcolare l’efficienza di funzionamento dei macchinari di uno stabilimento.
Un eccesso di scarti in produzione potrebbe essere sintomo di una cattiva calibratura della OEE, la metrica di efficienza di una macchina, linea o impianto produttivo, la quale è calcolata in valore percentuale dalla moltiplicazione di questi tre parametri: disponibilità, performance, qualità. Cosa indicano questi valori? Vediamolo qui di seguito:
- Disponibilità: è un indicatore di performance calcolato sul rapporto tra tempo di esecuzione reale e tempo di produzione pianificato.
- Performance: le prestazioni di una macchina si misurano tenendo conto di tutto ciò che interrompe il processo di produzione determinando una velocità inferiore a quella massima.
- Qualità: si calcola a partire dal numero di pezzi prodotti che non soddisfano gli standard di qualità. Avremo così i ‘pezzi buoni’ conformi allo standard produttivo e quelli difettosi che hanno bisogno di una rilavorazione.
Più schematicamente possiamo riassumere così:
- Disponibilità = tempo di esecuzione / tempo di produzione pianificato.
- Performance = (tempo ciclo ideale x conteggio totale pezzi prodotti) / tempo di esecuzione.
- Qualità = conteggio pezzi buoni / conteggio totale pezzi prodotti.
Il prodotto dato dalla moltiplicazione “Disponibilità x Prestazioni x Qualità” dà come risultato la misura dell’OEE. Ecco perché, a una percentuale alta di OEE corrisponde una performance efficiente delle macchine utensili e di tutta la linea di produzione.
Come si apprezza dal calcolo della OEE, il ruolo giocato dalla variabile “Tempo” è fondamentale per individuare eventuali inefficienze sulla base del rapporto che avremo tra tempo di produzione pianificato e tempo di arresto delle macchine non pianificato.
KPI principali per tracciare l’efficienza produttiva
Anche i fermi macchina infatti concorrono a penalizzare il valore di OEE. Più è alto il suo punteggio (in valori percentuali) e più il traguardo dell’efficienza produttiva sarà vicino. Monitorare in tempo reale attraverso i giusti KPI le prestazioni delle macchine o centri di lavoro è l’unico modo per scovare la quantità di problemi da risolvere. Tra questi sono da segnalare quelli definiti come i “Big Losses”, ovvero le grandi voci perdita annidate in ogni processo produttivo:
- i guasti;
- i cambi lotto/prodotto (setup);
- le rilavorazioni;
- gli sfridi, pezzi difettosi;
- le perdite di velocità della macchina;
- le microfermate.
Queste sacche di inefficienza vanno tenute sotto controllo attraverso la scelta dei giusti KPI.
Oltre alla OEE infatti esistono numerosi altri indicatori di performance che orientano nella misura di qualità di un processo produttivo nella sua totalità, come ad esempio:
- Il Work in Progress: misura il valore delle materie prime che entrano nel processo di produzione prima di ottenere il prodotto finito. WIP = Lead time di produzione x Valore del flusso di produzione.
- Tasso di fermo macchina: fornisce il rapporto tra interruzioni programmate e non programmate.
- Costo per unità: supporta il sistema di produzione nell’ottimizzazione dei costi. Formula CPU = Costi diretti dei materiali + Costi diretti della manodopera + Spese generali di produzione / Unità prodotte.
- Rendimento o First Time Through: misura l’efficienza e la qualità della produzione attraverso il numero di unità prodotte senza difetti rispetto al totale dei pezzi.
- Tempo medio tra i guasti: è la misura di quanto tempo intercorre tra un guasto e un altro durante la fase di produzione.
- Costi manodopera: quanto tempo viene speso effettivamente nell’operatività rispetto ai periodi di inattività?
- Tempo di Takt: misura la media tra il tempo di lavorazione di un’unità e quello dell’unità successiva.
- Costo evitato: è un indicatore del risparmio basato su misure preventive. Ossia, quanto i costi in attività di manutenzione hanno generato un saving. Costo di riparazione + Perdite di produzione – Costo di manutenzione preventiva = Costo evitato.
Più in generale, è opportuno introdurre tra i nostri indicatori tutte quelle piccole o grandi inefficienze che causano una minore produttività rispetto alla produzione pianificata. Ossia ciò che genera un delta ‘x’ tra la Capacità Produttiva Disponibile (CPD) “in teoria” e la produttività direttamente misurata sul campo.
La Capacità Produttiva Disponibile è anch’essa un KPI che fornisce una visione chiara sulla capacità produttiva di una macchina o di un impianto in relazione a un tempo prestabilito, quello di un turno di lavoro per fare un esempio. Si riferisce a un valore standardizzabile calcolato sul volume massimo di produzione nel pieno utilizzo delle ore disponibili. Da questa grandezza l’organizzazione procede solitamente a disegnare un planning di produzione, motivo per cui è cruciale evitare scostamenti importanti da questo valore.
L’efficienza in ambito produttivo è definibile anche come un rapporto tra un input e un output; cioè tra una risorsa a nostra disposizione e l’output che genera il suo corretto utilizzo. Questo rapporto descrive il valore effettivo della produttività aziendale.
Importanza dei dati nella misurazione dell’efficienza
Gli strumenti a disposizione delle imprese al giorno d’oggi abilitano una raccolta dati in tempo reale per identificare inefficienze e migliorare la produttività. I nuovi device, la sensoristica applicata alle macchine e i dati generati dai MES, o raccolti da altri layer tecnologici, sono diventati il punto di partenza per mettere a frutto strategie di miglioramento basate sull’analisi di grandi quantità di informazioni.
Le imprese manifatturiere che per anni si sono contraddistinte dalla concorrenza per l’implementazione della Lean production nelle loro linee, con l’avvicendarsi delle nuove tecnologie hanno avuto la possibilità di misurare l’efficienza delle macchine in tempo reale. Molte di queste hanno così sviluppato i propri sistemi, formando il personale e coinvolgendo consulenti esperti nella metodologia Lean Six Sigma,nell’efficientamento del processo.
Strategie per ottimizzare l’efficienza produttiva
Senza informazioni accurate sui tempi di inattività e sui fermi macchina non si può misurare l’efficienza produttiva in tempo reale o sapere quanto davvero siano produttive le linee di uno stabilimento. L’annotazione manuale delle possibili anomalie affidata solo ai lavoratori è un’attività esposta ad elevato rischio errore dal momento che spesso è proprio così che si trascurano gli episodi di inattività più brevi (i.e. microfermate). Moltiplicati durante tutto l’anno, questi fermi macchina temporanei che passano inosservati si possono trasformare in ore di stop non segnalate. L’utilizzo di dispositivi IoT nella misurazione continua e automatica delle inefficienze elimina invece il problema delle misurazioni manuali, garantendo un flusso continuo di dati.
Migliorare l’OEE per una maggiore efficienza
Il tema della tecnologia IoT è direttamente collegato anche a quello della manutenzione, la quale svolge un ruolo cruciale nel garantire il funzionamento regolare ed efficiente delle macchin .
Fare manutenzione non deve essere relegato a un compito di secondaria importanza, poiché da questa operazione dipende in ultima analisi non solo l’affidabilità e la longevità delle attrezzature, ma anche il valore stesso della OEE. Motivo per cui, mettere in agenda attività di questo tipo rappresenta un investimento strategico in grado di agire su leve di differente calibro come l’aumento di efficienza, la razionalizzazione dei costi senza dimenticare altri aspetti che includono compliance normativa, riduzione tempi di fermo macchina e aumento del ciclo di vita dei macchinari.