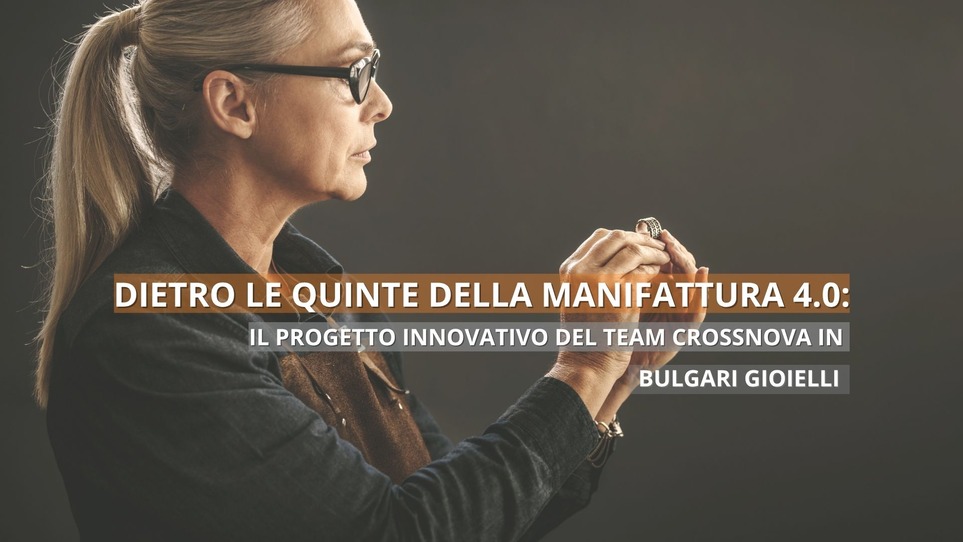
Dietro le quinte della manifattura 4.0: il progetto innovativo del team Crossnova in Bulgari Gioielli
Nel mondo della manifattura moderna, l’innovazione non è solo una questione di tecnologia: è un ecosistema fatto di persone, competenze e processi ottimizzati. Il progetto, sotto presentato, è stato condotto da Crossnova, in collaborazione con il Team Manufacturing di Bulgari Gioielli e racconta proprio questo: un viaggio concreto dentro una fabbrica intelligente, dove digitalizzazione e collaborazione sono i veri motori del cambiamento.
Un progetto reale di innovazione industriale
Il video ci porta all’interno di uno dei progetti chiave, sviluppato da Crossnova, nel settore Manufacturing 4.0, dove automazione, analisi dei dati e lean production si integrano in un flusso coerente e sostenibile. Tre protagonisti di Bulgari Gioielli – Omar Carrozzo (Team Manufacturing Coordinator), Federica Martinotti e Salvatore Petrantoni (Manufacturing Engineers) – raccontano lo sviluppo e l’implementazione di un nuovo sistema di gestione e controllo dei processi produttivi.
L’obiettivo?
Ottimizzare il flusso produttivo, ridurre sprechi e aumentare la qualità finale, mantenendo la centralità del fattore umano.
I pilastri del progetto: tra tecnologia e organizzazione
1. Coordinamento e pianificazione strategica
Come ci spiega Omar Carrozzo, la prima sfida è stata costruire un sistema di coordinamento efficiente, in grado di gestire in modo dinamico risorse umane, materiali, impianti e tempi di produzione. In un contesto industriale in rapida evoluzione, con richieste di mercato sempre più frammentate e cicli di vita dei prodotti ridotti, non basta più affidarsi a una pianificazione statica: serve flessibilità operativa e capacità decisionale in tempo reale.
Per affrontare questa sfida, è stato introdotto un sistema strutturato di KPI (Key Performance Indicators), progettati per misurare ogni fase del processo in modo trasparente, oggettivo e immediato.
I principali ambiti monitorati includono:
- Avanzamento produzione, con aggiornamenti costanti sull’avanzamento delle commesse e stato delle lavorazioni
- Indici di qualità, basati sull’analisi di conformità dei pezzi, segnalazioni di difetti e feedback del controllo qualità
- Scarti e inefficienze, con tracciabilità puntuale delle cause, per facilitare analisi di tipo root cause e azioni correttive rapide
- Tempi di attrezzaggio, un indicatore critico per la riduzione dei tempi morti nei cambi formato e nella riconfigurazione delle linee
Grazie a questa architettura, ogni figura coinvolta – dal planner all’operatore, fino al responsabile di reparto – dispone oggi di una visione chiara e condivisa dello stato produttivo, utile non solo per reagire agli imprevisti ma soprattutto per prevenire le inefficienze.
“Solo ciò che si misura si può migliorare”, sottolinea Omar. Ed è proprio da questa logica di misurazione continua che nasce l’impostazione “smart” della nostra produzione: non una fabbrica che rincorre i problemi, ma un sistema che li anticipa, li comprende e li trasforma in opportunità di miglioramento.
L’adozione di questa metodologia ha già portato a benefici concreti, tra cui una maggiore puntualità delle consegne, una riduzione degli sprechi e una crescita costante del livello di servizio verso i clienti finali.
2. Ingegneria di processo e simulazione digitale
Il cuore tecnologico del progetto è stato affidato a Federica Martinotti e Salvatore Petrantoni, ingegneri di produzione con una forte competenza in progettazione meccanica, automazione e ottimizzazione dei processi. Il loro lavoro ha rappresentato un punto di svolta per il reparto, grazie all’integrazione di strumenti digitali e approcci avanzati di industrial engineering.
- Il primo step è stato la modellazione CAD 3D delle attrezzature. Utilizzando software evoluti di progettazione, il team ha creato modelli digitali altamente dettagliati delle postazioni di lavoro, delle attrezzature custom e dei layout di linea. Questo ha consentito una visualizzazione tridimensionale preventiva dell’intero ciclo produttivo, rendendo possibile identificare criticità ergonomiche, spazi non ottimizzati e interferenze meccaniche già in fase di progettazione
- Successivamente, i modelli CAD sono stati integrati in software di simulazione dei flussi produttivi, che permettono di replicare digitalmente ogni fase del processo: dal carico dei materiali alla movimentazione interna, fino all’output finale. Grazie a queste simulazioni, è possibile prevedere colli di bottiglia, verificare la saturazione delle risorse e testare scenari alternativi di produzione, il tutto senza fermare nemmeno per un minuto la linea reale
Uno degli aspetti più innovativi è stato lo sviluppo di celle semi-automatizzate, progettate su misura in base al tipo di prodotto e al volume richiesto. Queste celle integrano sensoristica IoT, che consente il monitoraggio costante di parametri come temperatura, pressione, tempo ciclo e stato macchina. I dati raccolti vengono analizzati in tempo reale per identificare anomalie, ottimizzare le prestazioni e alimentare sistemi di manutenzione predittiva.
Fondamentale, in tutto questo, è stata anche l’attenzione all’interfaccia uomo-macchina (HMI). Federica e Salvatore hanno progettato postazioni che mettono l’operatore al centro: controlli semplificati, visualizzazioni intuitive, avvisi visivi e acustici, tutto pensato per rendere l’esperienza utente più fluida e sicura possibile. L’obiettivo non è sostituire il lavoro umano, ma potenziarlo, migliorandone precisione, ergonomia e benessere operativo.
Grazie a questa impostazione progettuale avanzata, ogni nuova linea produttiva viene oggi testata virtualmente prima di essere realizzata fisicamente. Questo approccio, tipico dei modelli digital twin, consente non solo di ridurre i tempi e i costi di sviluppo, ma anche di ottenere una maggiore affidabilità e ripetibilità nella produzione. Le modifiche progettuali possono essere testate e validate in ambienti simulati, evitando errori e rilavorazioni in fase di avviamento.
In sintesi, il contributo di Federica e Salvatore ha reso possibile una vera trasformazione digitale del processo produttivo, combinando innovazione tecnologica e attenzione al valore umano in modo armonico e strategico.
3. Automazione intelligente e raccolta dati
La vera svolta è l’integrazione tra automazione e raccolta dati. Ogni macchina è interconnessa e comunica con il sistema centrale, permettendo:
- Monitoraggio in tempo reale delle performance
- Tracciabilità completa del prodotto
- Interventi predittivi e manutenzione programmata
Non si tratta di sostituire le persone, ma di affiancarle con strumenti che rendono il lavoro più preciso, sicuro ed efficace.
Le persone al centro: formazione e collaborazione
Un aspetto centrale del progetto è la valorizzazione delle competenze interne. Il team ha lavorato in sinergia con gli operatori di linea, coinvolgendoli in ogni fase:
- Analisi condivisa delle criticità
- Workshop di miglioramento continuo
- Percorsi di formazione tecnica e digitale
Questo approccio partecipativo ha generato engagement e ownership: chi lavora sulle macchine è anche parte attiva dell’innovazione.
I risultati: benefici concreti per azienda e clienti
Dopo mesi di progettazione, test e implementazione, i risultati sono tangibili:
- Riduzione del lead time del 18%
- Diminuzione degli scarti produttivi del 25%
- Aumento del livello qualitativo percepito dal cliente finale
- Maggiore flessibilità nella gestione dei piccoli lotti e delle personalizzazioni
Questi numeri confermano come l’innovazione nei processi produttivi possa generare valore reale, non solo per l’azienda ma anche per l’intero ecosistema industriale.
Crossnova come modello di manifattura 4.0
Questo progetto rappresenta molto più di un caso di efficientamento produttivo: è la dimostrazione concreta di come Crossnova stia dando forma a una visione evoluta e autentica dell’Industria 4.0. Non si tratta solo di introdurre tecnologie avanzate, ma di costruire un modello organizzativo e culturale capace di trasformare la fabbrica in un ecosistema intelligente, sostenibile e orientato al futuro.
Collaborazione interfunzionale: Alla base di ogni progetto Crossnova c’è un forte lavoro di squadra trasversale. Manufacturing, Engineering, Qualità, Logistica e IT lavorano in stretta sinergia, superando le tradizionali barriere funzionali. Le decisioni non vengono più prese “a compartimenti stagni”, ma nascono da un confronto continuo tra reparti, stimolato da processi decisionali agili, metodi visuali e momenti strutturati di allineamento operativo.
Questa cultura della collaborazione interfunzionale è il vero acceleratore dell’innovazione: quando le competenze si incontrano, nascono soluzioni migliori e più rapide.
Decisioni guidate dai dati: La fabbrica moderna è anche – e soprattutto – data-driven. In Crossnova, ogni attività critica è monitorata da una rete di sensori, software e KPI, che alimentano dashboard in tempo reale e strumenti di analisi predittiva. Questo consente di prendere decisioni basate su dati oggettivi anziché su impressioni, riducendo l’incertezza e aumentando l’efficienza. Dall’andamento di una linea alla qualità di un lotto, dai tempi di attrezzaggio alle performance energetiche: tutto è tracciato, analizzato e trasformato in conoscenza operativa. Non è tecnologia fine a sé stessa, ma intelligenza applicata al miglioramento continuo.
Sostenibilità nei processi: Innovare significa anche produrre meglio, non solo di più. Il progetto ha introdotto pratiche mirate a ridurre sprechi, consumi e impatti ambientali. L’automazione intelligente consente un uso più efficiente delle risorse, mentre il monitoraggio costante aiuta a minimizzare gli scarti e a identificare aree di recupero. In parallelo, la progettazione delle linee tiene conto di aspetti ergonomici e di sicurezza, a vantaggio non solo dell’ambiente ma anche delle persone che ogni giorno operano in reparto. La sostenibilità, per Crossnova, è una leva competitiva, ma anche una responsabilità etica e sociale.
Crescita delle persone: Infine – ma forse prima di tutto – l’innovazione in Crossnova parte dalle persone. Ogni progetto è anche un’opportunità di crescita professionale: il team viene coinvolto attivamente, formato su nuove tecnologie e incoraggiato a proporre idee. L’adozione di strumenti digitali non sostituisce il lavoro umano, ma lo potenzia: riduce le attività ripetitive e libera tempo per attività a maggiore valore aggiunto.
Questa attenzione allo sviluppo delle competenze si traduce in un ambiente di lavoro più dinamico, stimolante e partecipativo, dove ognuno può contribuire al successo comune.
Una fabbrica connessa, intelligente e umana. È proprio da questa combinazione di tecnologia, cultura organizzativa e visione condivisa che nasce l’identità produttiva di Crossnova. Un’identità costruita giorno dopo giorno, con metodo e passione, per dare vita a una fabbrica connessa, intelligente e profondamente umana.
Qui, l’Industria 4.0 non è uno slogan, ma un modo concreto di operare, decidere e crescere insieme.
📌 Scopri come l’innovazione può trasformare i processi produttivi della tua fabbrica!