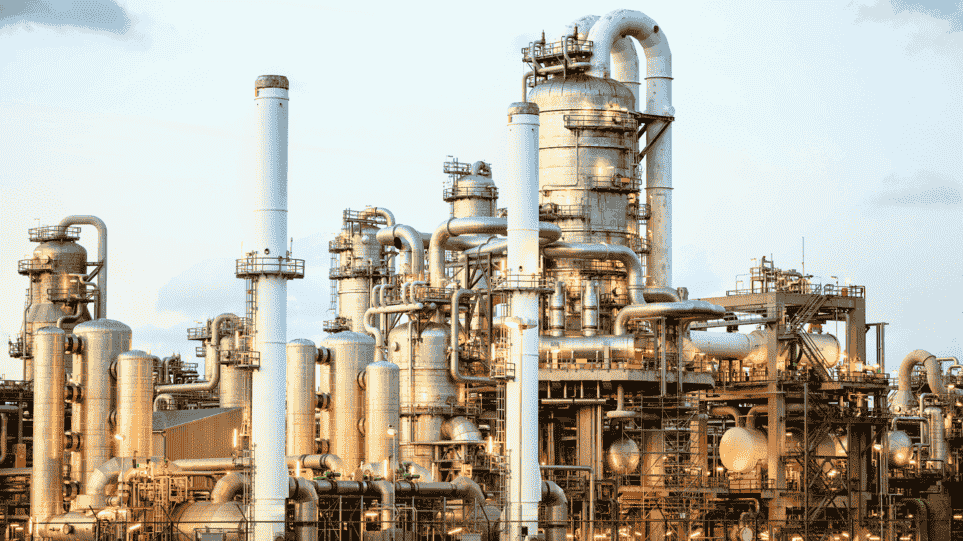
Strategie di ottimizzazione dei processi produttivi chimici con il Cost Deployment
In un contesto industriale caratterizzato da forti pressioni sui margini di profitto e dall’esigenza sempre più stringente di mantenere un alto livello di competitività, le aziende affrontano sfide significative nell’ottimizzazione delle risorse. La nostra è un’epoca in cui l’efficienza produttiva non è solo una questione di costi, ma anche di sostenibilità e reattività al mercato. Per questo motivo, è fondamentale che le organizzazioni individuino strategie capaci di aumentare la produttività, ridurre gli sprechi e garantire un costante allineamento agli standard qualitativi. Per questa azienda, può essere utile ottimizzare i processi produttivi chimici con il Cost Deployment.
- Questo è particolarmente vero per il settore chimico, dove la gestione efficace delle risorse, la minimizzazione degli scarti e l’ottimizzazione dei costi di produzione rappresentano elementi chiave per mantenere una posizione stabile sul mercato. Le aziende chimiche operano con margini spesso più ridotti rispetto ad altri settori, a causa della natura complessa dei processi e dei materiali impiegati, così come per le norme ambientali e di sicurezza molto rigorose che richiedono investimenti significativi. In questo contesto, le strategie di ottimizzare i processi produttivi chimici possono fare la differenza tra la crescita e il declino.
Scenario di riferimento
L’azienda chimica in analisi è di medie dimensioni, con 214 dipendenti e un fatturato annuo di 80 milioni di euro. Il suo obiettivo principale è rappresentato dall’ottimizzazione della linea produttiva più critica. Con margini di guadagno sempre più sotto pressione e una domanda di mercato che richiede flessibilità e qualità costante, l’azienda ha intrapreso un’iniziativa strutturata per migliorare il flusso di produzione e rendere più efficiente l’intero processo operativo.
- In questo Business Case, esploreremo l’applicazione della metodologia Cost Deployment, uno strumento potente per la riduzione e il controllo dei costi. Il progetto mirava a identificare le principali fonti di inefficienza nella linea produttiva, intervenendo per migliorare i processi, ridurre i costi operativi e ottenere una maggiore fluidità nella produzione senza compromettere la qualità del prodotto finale. La metodologia Cost Deployment si è rivelata ideale per raggiungere questi obiettivi, offrendo un framework strutturato e replicabile per l’identificazione e la classificazione delle perdite, che permette di ottenere un’efficienza produttiva tangibile e di sostenere l’azienda in un percorso di Miglioramento Continuo. Il Cost Deployment è ideale per ottimizzare i processi produttivi chimici.
Che cos’è il Cost Deployment?
La metodologia Cost Deployment è uno strumento avanzato di analisi e ottimizzazione dei costi che mira a massimizzare l’efficienza delle attrezzature e dei processi produttivi. Questa metodologia è stata progettata per supportare le aziende nell’identificazione sistematica delle inefficienze presenti nelle operazioni produttive, intervenendo sui costi nascosti che, se non gestiti, possono erodere i margini di profitto e ridurre la competitività aziendale. Si presta bene a ottimizzare i processi produttivi chimici.
Il Cost Deployment si basa su un’analisi approfondita e una classificazione dettagliata delle principali perdite operative. Questa classificazione aiuta l’azienda a identificare le aree di intervento prioritario, mettendo in evidenza gli ambiti con il maggior potenziale di risparmio. Attraverso un’accurata suddivisione, le perdite vengono categorizzate in macroaree come:
- Difetti di qualità – Per esempio, prodotti finiti o semilavorati che non rispettano gli standard richiesti e devono essere scartati o rilavorati, con costi aggiuntivi sia di materiale che di manodopera.
- Scarti di materiale – Perdite derivanti da sprechi di materie prime, sovrapproduzione o errori durante il processo di lavorazione. Gli scarti non solo aumentano i costi di produzione, ma influenzano anche la sostenibilità aziendale.
- Inefficienze della manodopera – Tempi morti, disorganizzazione dei turni, o una cattiva gestione delle risorse umane possono portare a perdite di produttività e costi aggiuntivi.
- Utilizzo non ottimale delle attrezzature – Tempi di inattività imprevisti, attrezzature obsolete o sottoutilizzate rappresentano un costo importante per l’azienda. Questo è particolarmente vero nel settore chimico, dove le attrezzature sono spesso specifiche e ad alta intensità di capitale.
Quantificazione e impatto economico delle perdite nei processi produttivi chimici
Un aspetto chiave del Cost Deployment è la capacità di tradurre ogni tipo di perdita in un valore economico preciso. Questa quantificazione permette di visualizzare chiaramente l’impatto di ciascuna inefficienza sul costo totale della produzione. L’azienda può così valutare con precisione dove intervenire per ottenere i massimi benefici in termini di riduzione dei costi.
Per esempio, se l’analisi rivela che gli scarti di materiale incidono per il 25% sui costi di produzione, l’azienda potrà sviluppare piani mirati per ridurre questa percentuale, migliorando i controlli di qualità e ottimizzando il processo produttivo. Questo calcolo dell’impatto economico non solo facilita la presa di decisioni, ma rende anche misurabile il ritorno sugli investimenti (ROI) delle iniziative di miglioramento intraprese.
Identificazione dei “costi nascosti” nei processi produttivi chimici
Un altro vantaggio distintivo della metodologia è la sua capacità di mettere in luce i “costi nascosti”. Questi sono costi che, pur non essendo immediatamente visibili, incidono in modo significativo sui risultati economici dell’azienda. Esempi di costi nascosti possono essere i tempi di fermo non pianificati delle attrezzature, le ore di lavoro straordinarie per riparazioni d’emergenza o i costi legati a spedizioni extra per compensare ritardi.
Il Cost Deployment permette di portare alla luce queste spese occulte, trasformandole in obiettivi di miglioramento misurabili. Una volta identificati, questi costi nascosti possono essere affrontati con piani di intervento specifici, che mirano alla riduzione delle inefficienze senza compromettere la qualità del prodotto finale.
Costruzione di una cultura di Miglioramento Continuo
L’applicazione del Cost Deployment non è solo una questione di risparmio economico, ma anche un metodo per costruire una cultura aziendale orientata al Miglioramento Continuo e alla consapevolezza dei costi. Coinvolgendo i dipendenti in ogni fase del processo – dalla raccolta dei dati alla fase di implementazione – il Cost Deployment promuove una maggiore responsabilità e consapevolezza tra i collaboratori, che diventano parte attiva nel processo di miglioramento. La metodologia spinge ogni reparto a contribuire in modo collaborativo al raggiungimento degli obiettivi di efficienza e di riduzione dei costi. Questo approccio partecipativo aumenta il livello di motivazione e coinvolgimento dei dipendenti, che vedono concretamente l’impatto del loro lavoro sugli obiettivi aziendali.
Un approccio flessibile e adattabile del Cost Deployment
Un ulteriore vantaggio del Cost Deployment è la sua flessibilità. Sebbene sia nata per l’industria manifatturiera, questa metodologia si adatta a diverse tipologie di produzione, indipendentemente dalla complessità dei processi o dal tipo di prodotti realizzati. Nel caso specifico dell’azienda chimica in esame, il Cost Deployment ha permesso di identificare rapidamente le aree di maggior perdita e di implementare soluzioni mirate, con risultati significativi in termini di efficienza e riduzione dei costi operativi. La metodologia ha portato ad ottimizzare i processi produttivi chimici.
L’azienda e l’iniziativa di miglioramento grazie al Cost Deployment
L’azienda chimica protagonista di questo Business Case è specializzata nella produzione di una vasta gamma di prodotti per il mercato industriale e commerciale. L’offerta dell’azienda include composti chimici utilizzati in molteplici settori, e la flessibilità di produzione è fondamentale per rispondere alle diverse esigenze dei clienti. Con una linea produttiva ad alta capacità, l’azienda deve però fronteggiare sfide significative, tra cui:
- Tempi di inattività delle attrezzature: Gli impianti, complessi e soggetti a rigorosi controlli di sicurezza, richiedono frequenti interventi di manutenzione. Ridurre i tempi di inattività non pianificati e migliorare l’affidabilità delle macchine è essenziale per garantire una produzione continua ed efficiente.
- Qualità dei materiali e degli output: Nel settore chimico, la qualità delle materie prime e la precisione del processo produttivo influiscono direttamente sulla qualità del prodotto finale. Difetti nei lotti di produzione possono portare a scarti costosi o a rilavorazioni onerose.
- Gestione dei costi di produzione: La produzione chimica ha costi fissi e variabili elevati, che includono non solo l’acquisto delle materie prime, ma anche i costi legati all’energia, alla gestione degli scarti e alle normative ambientali. Ottimizzare questi costi senza compromettere la qualità è un obiettivo chiave per l’azienda.
Per affrontare queste sfide, l’azienda ha deciso di avviare un’iniziativa di miglioramento strutturata, focalizzandosi sulla metodologia Cost Deployment. Un team multidisciplinare, composto da membri dell’area ingegneristica, della produzione e della qualità, ha lavorato per identificare le principali fonti di perdita lungo la linea produttiva. Il loro obiettivo era analizzare ogni aspetto del processo per eliminare le inefficienze e ottenere una maggiore fluidità operativa.
Gli obiettivi dell’iniziativa di miglioramento per ottimizzare i processi produttivi chimici
CROSSNOVA ha avviato un’iniziativa per ottimizzare i processi produttivi chimici con il Cost Deployment. L’intento era raggiungere obiettivi chiari e misurabili, orientati al miglioramento delle prestazioni produttive e alla riduzione dei costi operativi. In particolare, l’approccio ha permesso di focalizzarsi su tre macro-obiettivi strategici, ognuno mirato a rispondere alle principali sfide operative dell’azienda. Di seguito, una descrizione dettagliata dei principali obiettivi dell’iniziativa.
Riduzione dei tempi di inattività
Uno degli obiettivi principali del progetto era quello di ridurre i tempi di inattività delle attrezzature, poiché i fermi macchina non pianificati rappresentano una delle principali fonti di inefficienza e di perdita economica. Attraverso l’analisi dei dati storici di produzione e il monitoraggio continuo in tempo reale, il team è riuscito a identificare i fattori principali che causavano interruzioni non programmate. Tra questi, i problemi più ricorrenti includevano usura delle attrezzature, guasti improvvisi e inefficienze nel processo di manutenzione reattiva.
Sulla base di queste informazioni, l’azienda ha sviluppato e implementato un piano di manutenzione predittiva, introducendo sensori e tecnologie di monitoraggio avanzato che permettono di rilevare i segni di deterioramento delle attrezzature prima che si trasformino in guasti. Inoltre, il personale è stato formato per interpretare i dati di monitoraggio e intervenire preventivamente. Grazie a queste misure, l’azienda ha ridotto significativamente i tempi di inattività, aumentando la disponibilità delle attrezzature e migliorando la fluidità del processo produttivo.
Miglioramento della qualità del prodotto
Un altro obiettivo chiave dell’iniziativa era il miglioramento della qualità del prodotto finito, una priorità cruciale per qualsiasi azienda chimica che deve mantenere standard qualitativi rigorosi. La metodologia Cost Deployment ha permesso di identificare e analizzare le principali cause dei difetti di produzione, che includevano la variabilità nella qualità delle materie prime, le discrepanze nei dosaggi e l’incapacità di mantenere parametri di processo costanti.
Per affrontare queste criticità, l’azienda ha introdotto interventi mirati in più aree, tra cui:
- Controllo delle materie prime: Il team ha collaborato con i fornitori per garantire una qualità costante delle materie prime, e sono stati introdotti controlli di qualità più stringenti in fase di accettazione dei materiali.
- Automazione dei dosaggi: È stato installato un sistema di automazione dei dosaggi per migliorare la precisione delle miscele chimiche e ridurre il margine di errore umano. Questo ha consentito di ottenere una maggiore uniformità nei lotti di produzione.
- Monitoraggio continuo dei parametri critici: Parametri come temperatura, pressione e composizione chimica vengono ora monitorati costantemente tramite sensori. Gli operatori sono in grado di intervenire tempestivamente per correggere eventuali scostamenti, riducendo gli scarti e le rilavorazioni.
Questi interventi hanno portato a una riduzione significativa degli scarti e a un miglioramento della conformità agli standard qualitativi, garantendo così un prodotto finito più stabile e affidabile, apprezzato dai clienti.
Ottimizzazione dei costi operativi
L’ottimizzazione dei costi operativi rappresentava un obiettivo cruciale per aumentare la competitività dell’azienda e migliorare la sostenibilità economica e ambientale del processo produttivo. L’analisi del Cost Deployment ha rivelato varie fonti di costi nascosti e inefficienze che potevano essere eliminate o ridotte. Questi costi includevano lo spreco di materie prime, il consumo eccessivo di energia e i costi legati alla gestione dei rifiuti chimici.
Per affrontare queste inefficienze, il team ha implementato diverse soluzioni:
- Ottimizzazione dell’uso delle materie prime: Sono stati studiati i processi di dosaggio e miscelazione per garantire l’uso ottimale dei materiali, minimizzando scarti e riducendo il volume delle materie prime non necessarie.
- Riduzione degli sprechi di energia: Sono state introdotte tecnologie di monitoraggio energetico per identificare e correggere le aree di consumo elevato. Grazie a questo sistema, l’azienda ha potuto programmare interventi mirati, come la manutenzione degli impianti di ventilazione e l’adozione di orari di funzionamento più efficienti per le apparecchiature ad alto consumo.
- Miglioramento della gestione dei rifiuti chimici: Per ridurre i costi di smaltimento e migliorare la sostenibilità ambientale, l’azienda ha adottato pratiche di gestione dei rifiuti più efficienti e ha ridotto la quantità di materiali di scarto generati durante il processo di produzione.
L’adozione di tecnologie di monitoraggio e automazione ha quindi permesso all’azienda di ottenere un impatto positivo sia sui costi che sull’impatto ambientale, consolidando così il suo impegno verso una produzione sostenibile. L’azienda è riuscita a ottimizzare i processi produttivi chimici con il Cost Deployment. Il risparmio economico ottenuto ha reso possibile investire ulteriormente in innovazioni tecnologiche, migliorando così ulteriormente l’efficienza operativa e la competitività dell’azienda.
Il processo di implementazione del Cost Deployment
La metodologia Cost Deployment è stata implementata seguendo una struttura in fasi:
- Mappatura delle perdite
Il team ha iniziato raccogliendo dati dettagliati sul funzionamento della linea produttiva e sulle performance delle attrezzature. Sono stati analizzati i dati di produzione, i report di qualità e le informazioni sulla manutenzione, mappando ogni perdita significativa. - Quantificazione economica
Ogni categoria di perdita è stata valutata in termini di impatto economico, consentendo di identificare le aree con il maggior potenziale di risparmio. Questo ha permesso di dare priorità agli interventi, concentrando le risorse sui punti critici. - Definizione delle aree critiche di intervento
Dopo la fase di quantificazione, il team ha individuato le aree chiave che influenzavano maggiormente i costi e l’efficienza. Nel caso dell’azienda, i difetti di qualità, i tempi di inattività delle attrezzature e gli scarti di materiale sono emersi come principali fonti di inefficienza. - Sviluppo del piano di azione
In seguito, il team ha formulato un piano d’azione mirato, che includeva la formazione del personale per migliorare le competenze tecniche, l’adozione di nuove attrezzature per ridurre i tempi di cambio e l’implementazione di un sistema di monitoraggio in tempo reale della linea produttiva. - Monitoraggio Continuo e adattamento del piano
Una volta implementate le modifiche, l’iniziativa è stata accompagnata da un monitoraggio costante dei risultati. Questo ha permesso di valutare l’efficacia delle azioni intraprese e di effettuare aggiustamenti per mantenere i miglioramenti ottenuti nel tempo.
I benefici ottenuti grazie al Cost Deployment
L’applicazione della metodologia Cost Deployment ha portato a risultati tangibili. Dopo un anno dall’inizio del progetto, l’azienda ha ottenuto:
- Riduzione del 20% nei tempi di inattività. Il nuovo sistema di manutenzione predittiva ha contribuito a diminuire sensibilmente i fermi imprevisti delle attrezzature.
- Aumento della qualità del prodotto del 10%. Grazie all’adozione di controlli di qualità più rigorosi e all’ottimizzazione dei parametri di processo, l’azienda ha ridotto gli scarti e migliorato la conformità agli standard richiesti.
- Diminuzione dei costi di produzione del 15%. L’ottimizzazione dell’uso delle materie prime, l’efficientamento dei processi e la riduzione degli scarti hanno permesso all’azienda di ottenere un risparmio significativo nei costi operativi.
Considerazioni finali sul Cost Deployment
L’implementazione della metodologia Cost Deployment in questa azienda chimica ha dimostrato come una strategia di ottimizzazione strutturata possa portare a ottimizzare i processi produttivi chimici.
Il progetto ha non solo migliorato l’efficienza operativa e ridotto i costi, ma ha anche contribuito a creare una cultura di Miglioramento Continuo all’interno dell’organizzazione. Grazie a un approccio sistematico e al coinvolgimento attivo del personale, l’azienda ha potuto ottenere una maggiore consapevolezza sui costi e una maggiore competitività sul mercato.
Questo Business Case evidenzia i vantaggi del Cost Deployment come strumento di ottimizzazione per le aziende che operano in contesti complessi. In questi casi, il controllo dei costi e l’efficienza produttiva rappresentano elementi essenziali per il successo e la sostenibilità a lungo termine.
Se anche la tua azienda desidera ottimizzare i processi produttivi e ridurre gli sprechi, contattaci subito per saperne di più!