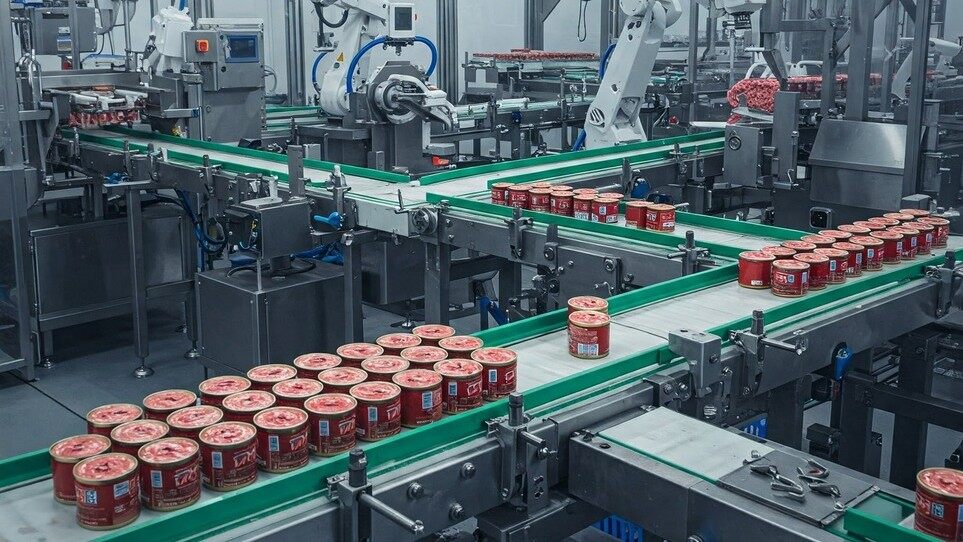
Come ridurre gli scarti produttivi e ottenere un risparmio annuale di 71.000€: il caso di successo nel settore alimentare
Nel settore altamente competitivo della grande distribuzione organizzata (GDO), ogni dettaglio del processo produttivo può fare la differenza. Ottimizzare le fasi di produzione non significa solo lavorare più velocemente o con meno risorse: vuol dire ridurre gli scarti produttivi, contenere i costi, migliorare la qualità del prodotto finito e aumentare significativamente la marginalità operativa.
In un contesto in cui la domanda dei consumatori è sempre più esigente e i margini sono spesso compressi, le aziende del comparto alimentare devono affrontare la doppia sfida di garantire efficienza interna e sostenibilità esterna. Riuscire a intervenire efficacemente sugli scarti produttivi – spesso sottovalutati o difficili da quantificare – rappresenta oggi un vero vantaggio competitivo.
In questo articolo raccontiamo un caso di successo concreto: quello di un’azienda leader nella produzione di carne in scatola, protagonista nella GDO, che ha saputo trasformare un problema critico – ovvero gli scarti elevati nella fase di inscatolamento – in una leva di crescita e ottimizzazione. Attraverso un progetto mirato di miglioramento dei processi, l’azienda ha raggiunto risultati straordinari nella riduzione degli sprechi, ottenendo al contempo un importante risparmio economico annuale.
Il problema: scarti fino al 2,9% nella fase di insacchettamento
L’azienda protagonista di questo caso di studio, attiva nella grande distribuzione organizzata (GDO) con un marchio storico di carne in scatola, si trovava ad affrontare una problematica produttiva rilevante: una percentuale di scarti giornalieri anomala, in particolare su formati critici, che raggiungeva in media il 2% del totale prodotto, con picchi massimi fino al 2,9%.
Questi valori risultavano ampiamente superiori alla soglia di tolleranza interna stabilita allo 0,35%, compromettendo l’efficienza dell’intero ciclo produttivo. Il problema si manifestava in modo marcato durante la fase di inscatolamento, una delle più sensibili del processo, dove si verificavano numerosi scarti legati a errori di dosaggio, difetti di chiusura o fuori specifica del prodotto.
Le ripercussioni sul piano operativo ed economico erano significative: oltre alla perdita diretta di materia prima, si registravano fermi linea, aumenti dei costi di produzione e una riduzione della marginalità per unità venduta. Inoltre, l’eccessivo volume di scarti metteva sotto pressione anche la logistica interna e il sistema di controllo qualità, costringendo l’azienda a un dispendioso rework o allo smaltimento del prodotto non conforme.
In un settore dove la precisione e la standardizzazione dei processi sono fondamentali, tali inefficienze rappresentavano un ostacolo serio per la crescita sostenibile e il raggiungimento degli obiettivi aziendali di produttività e qualità.
Le conseguenze: perdita di prodotto e costi elevati
Questa situazione di inefficienza aveva un impatto diretto e tangibile su diversi aspetti chiave della performance aziendale, compromettendo non solo la redditività, ma anche la reputazione del marchio e la capacità di garantire una produzione sostenibile e di qualità.
In particolare:
- Aumento dei costi di produzione: Lo spreco di materia prima generato dagli scarti comportava un innalzamento dei costi variabili, incidendo negativamente sul costo unitario del prodotto. Ogni grammo perso rappresentava un valore economico non recuperabile, a cui si sommavano i costi legati alla gestione dello scarto stesso (smaltimento, rilavorazioni, manutenzione straordinaria). L’effetto domino era evidente anche nella catena di approvvigionamento, che risultava sottoposta a maggiore pressione per garantire volumi sufficienti a coprire la parte di produzione persa;
- Riduzione della marginalità operativa: La crescita incontrollata degli scarti, soprattutto nei formati più critici, comprometteva in modo diretto la redditività del prodotto, riducendo il margine di guadagno per unità venduta. Questo rendeva difficile mantenere un equilibrio tra competitività commerciale e sostenibilità economica, soprattutto in un contesto di forte concorrenza sul prezzo come quello della GDO;
- Difficoltà nel rispetto degli standard aziendali di qualità e sostenibilità: L’elevato livello di scarti non solo metteva a rischio il mantenimento degli standard qualitativi interni, ma anche l’aderenza a parametri ambientali e normativi sempre più stringenti. Un eccesso di scarti si traduceva, infatti, in un aumento dell’impatto ambientale del ciclo produttivo, in contrasto con gli obiettivi aziendali di responsabilità sociale e sostenibilità ambientale. Inoltre, un processo produttivo non controllato esponeva l’azienda a potenziali non conformità e contestazioni da parte di clienti o enti certificatori.
La soluzione: ottimizzazione del processo e formazione del personale
Il cambiamento è stato possibile grazie all’intervento mirato del team Crossnova, che ha accompagnato l’azienda in un percorso di ottimizzazione dei processi produttivi, attraverso un progetto strutturato, personalizzato e orientato ai risultati. L’intervento si è basato su un’analisi approfondita delle criticità, seguita dalla definizione di azioni correttive concrete, condivise con il team operativo e implementate sul campo.
In particolare, grazie al supporto di Crossnova, l’azienda è riuscita a ottenere miglioramenti significativi e misurabili in tempi rapidi:
- Standardizzazione dei processi: sono state introdotte procedure operative chiare e replicabili, che hanno permesso di stabilizzare le prestazioni produttive e ridurre drasticamente le deviazioni. Il risultato è stato un abbattimento degli scarti giornalieri fino a un valore medio dello 0,18%, ben al di sotto della soglia di tolleranza interna del 0,35%, garantendo maggiore controllo e prevedibilità del processo.
- Riduzione dei costi e incremento dell’efficienza: l’intervento ha portato a una gestione più efficiente dei materiali, eliminando sprechi e riducendo i costi associati al riutilizzo o smaltimento del prodotto difettoso. Ne è conseguita una migliore performance operativa, con un impatto positivo anche sui margini economici.
- Formazione sul campo e cultura del Problem Solving: uno degli elementi distintivi dell’approccio Crossnova è stata la formazione pratica del personale di reparto, finalizzata a trasferire strumenti concreti di Problem Solving industriale. I team sono stati coinvolti attivamente nel riconoscere le cause degli scarti, proporre soluzioni e monitorare i risultati, favorendo la diffusione di una cultura proattiva e orientata al miglioramento continuo.
Grazie a questo progetto, non solo sono stati raggiunti obiettivi tecnici importanti, ma si è anche rafforzato il coinvolgimento delle risorse interne, oggi più consapevoli, autonome e preparate nella gestione dei processi.
I risultati: fino all’89% di scarti in meno
I risultati ottenuti al termine del progetto non lasciano spazio a dubbi: l’intervento ha generato una riduzione drastica e sostenibile degli scarti produttivi, con un impatto immediato su efficienza, costi e qualità. I dati parlano chiaro:
- Per il formato da 140 g, uno dei più soggetti a criticità, la percentuale di scarti è passata dal 1,719% iniziale al 0,185%, con una riduzione complessiva dell’89%.
- Per il formato da 90 g, il miglioramento è stato altrettanto significativo: gli scarti sono stati ridotti da 1,24% a 0,177%, pari a una riduzione dell’85%.
Questi risultati non solo hanno consentito all’azienda di rientrare abbondantemente nella soglia di tolleranza stabilita (0,35%), ma hanno anche rappresentato un punto di svolta nel controllo dei processi critici. La riduzione è stata ottenuta senza compromessi sulla velocità di produzione o sulla qualità del prodotto finito, dimostrando che è possibile coniugare produttività, qualità e sostenibilità attraverso un approccio metodico e orientato al miglioramento continuo.
In particolare, l’eliminazione delle variabili che generavano scarti – come errori di pesatura, microfermate o difetti di confezionamento – ha reso i processi più stabili, controllabili e ripetibili, con effetti positivi anche sulla pianificazione della produzione e sulla gestione delle risorse.
L’azienda ha potuto quindi trasformare un’area critica in un punto di forza, ottenendo vantaggi non solo economici, ma anche strategici, rafforzando la propria posizione competitiva nel mercato.
Il risparmio: +71.000€ annui
L’ottimizzazione dei processi produttivi, realizzata in collaborazione con il team Crossnova, ha portato a un risparmio economico annuale pari a 71.000 euro, frutto della significativa riduzione degli scarti nei formati più critici e di un generale miglioramento dell’efficienza operativa lungo tutta la linea produttiva.
Questo “saving strutturale”, non legato a tagli temporanei o azioni correttive isolate, è il risultato di un approccio metodico e strategico che ha permesso di intervenire sulle cause alla radice dello spreco. L’azienda è riuscita a ottimizzare il consumo di materia prima, ridurre le rilavorazioni e migliorare la pianificazione, con un impatto positivo e misurabile anche su produttività, sostenibilità e qualità percepita.
Ma il vero valore aggiunto del progetto risiede nella sua replicabilità e scalabilità: le competenze trasferite al personale, unite a un sistema di gestione più solido, consentiranno all’azienda di mantenere e consolidare nel tempo i risultati ottenuti, favorendo un percorso di miglioramento continuo.
Questo caso dimostra concretamente come l’ottimizzazione dei processi produttivi, unita a un investimento mirato nella formazione delle risorse umane, possa generare un impatto diretto sulla redditività aziendale, anche in contesti produttivi maturi o ad alta automazione. Una strategia vincente che fonde innovazione operativa, controllo dei processi e crescita sostenibile, in linea con le nuove sfide dell’industria alimentare e della GDO. In un mercato sempre più orientato all’efficienza e alla sostenibilità, questo intervento rappresenta un modello virtuoso di come problem solving, metodo e competenze condivise possano trasformare un punto debole in un vantaggio competitivo tangibile e duraturo.
📌 Ridurre gli scarti non è solo una questione di costi: è una leva strategica per aumentare l’efficienza, migliorare la qualità e rafforzare la competitività
Scopri come applicare il nostro metodo e ottenere risultati concreti e misurabili!