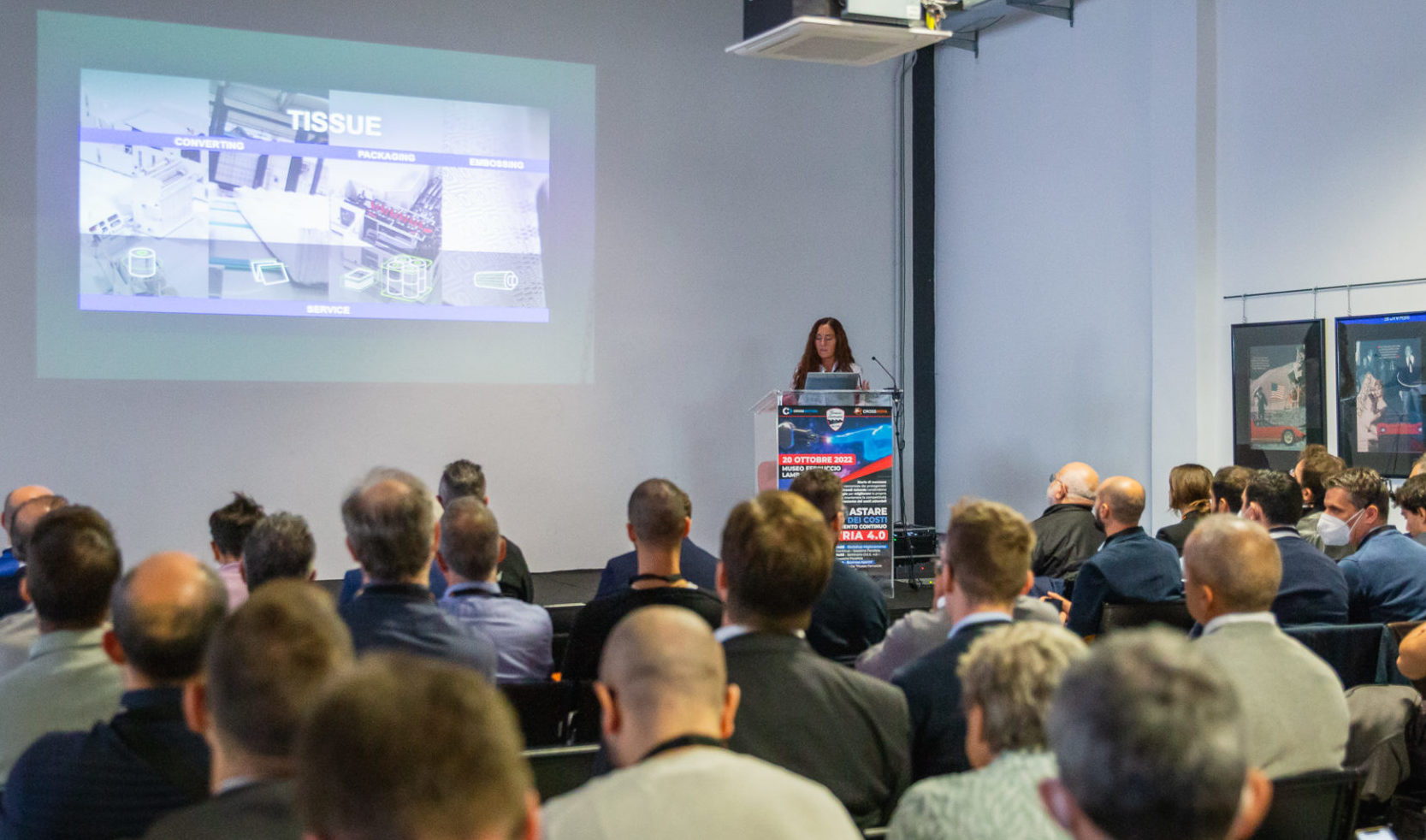
Come implementare un programma di Continuous Improvement efficace ed efficiente
In un contesto economico caratterizzato da rapidi cambiamenti e da un livello di competitività sempre più elevato, l’efficienza operativa e la capacità di adattamento sono diventate le chiavi per garantire la sostenibilità e il successo a lungo termine delle aziende. Oggi, il Miglioramento Continuo (Continuous Improvement, CI) non è solo una pratica gestionale, ma una leva strategica che consente alle aziende di innovare e ottimizzare i propri processi, migliorando costantemente la qualità, riducendo i costi e aumentando la soddisfazione dei clienti.
Un esempio virtuoso di questa filosofia è rappresentato da VALMET TISSUE CONVERTING, un leader globale nel settore della trasformazione della carta tissue. L’azienda è nota per la sua capacità di anticipare e soddisfare le esigenze del mercato attraverso tecnologie avanzate e attenzione costante all’efficienza. Progetta e produce macchinari e soluzioni all’avanguardia, che coprono l’intera catena del valore, dal converting al packaging, offrendo prodotti affidabili e sostenibili.
Alla base del successo di Valmet Tissue si trova un programma di Operational Excellence fondato sulla metodologia Lean Six Sigma avviato oltre dieci anni fa. Ha permesso di coinvolgere ogni area dell’azienda creando una cultura organizzativa che incoraggia l’innovazione e l’ottimizzazione dei processi a tutti i livelli. Oggi il Lean Six Sigma è un elemento fondante del DNA aziendale. Viene applicato quotidianamente in aree strategiche come la produzione, la qualità, la ricerca e sviluppo contribuendo al successo globale aziendale.
Per approfondire i risultati ottenuti e le sfide affrontate in questo percorso, abbiamo avuto il piacere di intervistare Daniela Altariva, HSE & Operational Excellence Manager.
Lean Six Sigma come parte integrante del DNA aziendale
Alla domanda su quanto la metodologia Lean Six Sigma venga applicata quotidianamente in azienda, Daniela Altariva risponde con entusiasmo, evidenziando come l’approccio sia ormai diventato una componente intrinseca del DNA di Valmet Tissue, permeando ogni aspetto dell’operatività aziendale.
“Abbiamo iniziato un percorso strutturato di formazione Lean Six Sigma circa dieci anni fa, integrato all’interno di un programma di Operational Excellence Global. Oggi contiamo un centinaio di risorse certificate Green Belt e una quindicina di Black Belt, distribuite in tutta la Business Area”. Daniela sottolinea come l’investimento sulla formazione del personale abbia creato esperti interni altamente qualificati, capaci di promuovere il miglioramento continuo in tutta l’organizzazione.
La diffusione capillare del Lean Six Sigma in ogni funzione aziendale garantisce infatti una costante eliminazione degli sprechi e un miglioramento continuo dei processi. Ogni giorno si utilizzano strumenti e tecniche strutturate per identificare e risolvere inefficienze, migliorare la qualità e ottimizzare le risorse. Questo approccio rigoroso è impiegato in tutte le funzioni aziendali, dalla produzione agli acquisti, fino alla qualità e alla manutenzione, assicurando che i miglioramenti non siano sporadici ma parte di un sistema operativo consolidato.
La metodologia si estende ben oltre le aree tradizionalmente operative e produttive, abbracciando anche funzioni meno convenzionali come il customer service e il marketing. In queste aree il Lean Six Sigma consente di analizzare i processi di risposta e gestione del cliente, riducendo tempi di attesa, ottimizzando le comunicazioni e migliorando la soddisfazione del cliente. Il marketing, dal canto suo, utilizza l’approccio data-driven del Six Sigma per sviluppare strategie mirate, identificando le esigenze specifiche dei clienti attraverso dati quantitativi e analisi di mercato.
In questo modo, il Lean Six Sigma aiuta Valmet Tissue Converting a costruire una cultura aziendale basata sulla proattività e sull’innovazione continua. Ogni dipendente, grazie alla formazione e alla consapevolezza condivisa, è incentivato a vedere e risolvere i problemi in modo strutturato, analizzando le cause alla radice e proponendo soluzioni concrete. Questo approccio ha creato una comunità di “problem solver” all’interno dell’azienda, dove ogni risorsa ha le competenze e gli strumenti per fare la differenza.
Lean Six Sigma nel settore dei Macchinari Industriali
Nel settore dei macchinari industriali, il Lean Six Sigma ha dimostrato di essere una metodologia particolarmente adatta per ottenere miglioramenti significativi, combinando strumenti lean focalizzati sulla riduzione degli sprechi con approcci quantitativi e analitici propri del Six Sigma. Questo equilibrio tra efficienza e controllo della qualità rende il Lean Six Sigma particolarmente utile in un contesto come quello dei macchinari industriali, dove precisione, affidabilità e ottimizzazione dei processi sono essenziali per garantire il successo aziendale e mantenere un vantaggio competitivo.
Daniela Altariva sottolinea come il Lean Six Sigma non solo permette di monitorare e migliorare i processi produttivi, ma facilita anche l’adattamento rapido a nuove richieste, che possono variare da una maggiore personalizzazione dei macchinari fino alla necessità di ridurre costi e tempi di consegna.
Nel campo dei macchinari industriali, ogni progetto o processo di produzione può presentare delle specificità tecniche che rendono cruciale l’approccio Lean Six Sigma. La flessibilità della metodologia permette di adattare le tecniche lean o gli strumenti di analisi Six Sigma alle esigenze specifiche del progetto. Ad esempio, strumenti come il Value Stream Mapping o il 5S possono essere utilizzati per ottimizzare il layout di produzione, ridurre i tempi di ciclo e migliorare il flusso dei materiali, mentre analisi statistiche avanzate e diagrammi di controllo tipici del Six Sigma consentono di monitorare e migliorare la qualità dei componenti o delle parti dei macchinari prodotti.
In un contesto in cui la qualità e la precisione sono imprescindibili, il Six Sigma offre un approccio rigoroso per ridurre la variabilità dei processi produttivi e migliorare la conformità delle specifiche tecniche, assicurando che i macchinari prodotti rispettino standard elevati e siano in grado di soddisfare le aspettative dei clienti più esigenti.
Il Lean Six Sigma, quindi, permette di ridurre al minimo difetti e scarti, migliorando la sostenibilità della produzione. Inoltre, offre vantaggi anche dal punto di vista della sicurezza e del coinvolgimento del personale. Applicare questa metodologia contribuisce a rendere i processi più sicuri ed efficienti, riducendo il rischio di errori e migliorando l’ambiente di lavoro. Per i dipendenti, l’introduzione del Lean Six Sigma crea un’opportunità di crescita professionale, poiché li coinvolge attivamente nella risoluzione dei problemi e nello sviluppo di soluzioni migliorative.
Grazie al Lean Six Sigma, le aziende del settore acquisiscono la flessibilità necessaria per rispondere rapidamente alle richieste di un mercato in continua evoluzione, riuscendo ad anticipare le tendenze e le aspettative del cliente finale. Questa metodologia si rivela quindi una strategia fondamentale per innovare e migliorare costantemente, rafforzando la capacità di adattamento dell’azienda e assicurandole un posizionamento di eccellenza nel settore.
Il valore del DMAIC: punti di forza e limiti
Uno dei pilastri della Lean Six Sigma è l’approccio DMAIC (Define, Measure, Analyze, Improve, Control), un framework che guida l’analisi e l’ottimizzazione dei processi. Daniela Altariva ne evidenzia il principale punto di forza.
“Il DMAIC permette di confutare le percezioni con i dati, rendendo l’analisi del processo oggettiva e obiettiva”. Questo approccio si rivela particolarmente utile per problemi di complessità medio-alta, dove la soluzione non è immediatamente evidente.
Nonostante la sua efficacia, l’approccio DMAIC presenta delle limitazioni. Quando la complessità del problema è limitata o il processo non richiede interventi strutturati, il DMAIC può risultare eccessivo e persino inefficace. In queste situazioni, approcci alternativi come il KAIZEN o il PDCA (Plan Do Check Act) risultano più adatti. Questi metodi, infatti, sono più agili e meno rigorosi, consentendo un miglioramento continuo che si adatta bene a contesti meno complessi o a cambiamenti incrementali.
Per i progetti di progettazione e implementazione di nuovi processi, invece, si consiglia di adottare la metodologia Design for Six Sigma (DFSS). Il DFSS si concentra sulla creazione di processi fin dall’inizio ottimizzati per la qualità e le performance. A differenza del DMAIC, il DFSS è orientato non alla correzione ma alla prevenzione, con l’obiettivo di costruire processi efficienti che riducano al minimo i difetti e gli sprechi già nella fase di progettazione.
In conclusione, grazie all’esperienza di CROSSNOVA, abbiamo maturato la consapevolezza che la scelta della metodologia più adatta – DMAIC, KAIZEN, PDCA o DFSS – dipende dal contesto specifico e dalla complessità del problema da risolvere. Adottare l’approccio corretto permette di massimizzare i benefici degli interventi e di raggiungere gli obiettivi di miglioramento in modo più efficace ed efficiente.
I vantaggi del Miglioramento Continuo e l’importanza della formazione
Per chi desidera avviare un percorso di Continuous Improvement, l’Operational Excellence Manager di Valmet Tissue non ha dubbi. Il Miglioramento Continuo è una scelta vincente per qualsiasi azienda, sia nel mondo del manufacturing che dei servizi. Tuttavia, sottolinea che il successo di un programma CI è strettamente legato alla formazione.
“Il programma di Miglioramento Continuo è imprescindibile dalla formazione, che porta soprattutto a un cambio di mindset delle persone. Questi agenti del cambiamento diventano i principali protagonisti dell’innovazione, portando vantaggi tangibili alle singole funzioni aziendali.”
La collaborazione con Crossnova: un valore aggiunto
Daniela Altariva conclude l’intervista con un feedback entusiasta sulla collaborazione con Crossnova. Evidenzia, infatti, come il supporto Crossnova abbia reso il percorso particolarmente stimolante. “Il team Crossnova ha saputo calarsi nella nostra specifica realtà aziendale, adattandosi alle nostre esigenze e comprendendo a fondo le sfide del nostro settore. Questa capacità di immedesimazione e personalizzazione è stata determinante nel garantire risultati concreti e duraturi”.
“Uno dei punti di forza della collaborazione con Crossnova è stato l’approccio su misura e la flessibilità che gli esperti hanno portato in ogni fase del progetto. Grazie a una profonda esperienza e al know-how sul miglioramento continuo, Crossnova ha saputo combinare teoria e pratica, adattando tecniche e strumenti in modo specifico per i processi e le esigenze di Valmet Tissue. Questo ha permesso di massimizzare l’efficacia degli interventi e di rendere il processo di miglioramento continuo più accessibile e comprensibile per tutti i team aziendali coinvolti”.
“Gli esperti di Crossnova non si sono limitati a portare conoscenze tecniche. Hanno instaurato un dialogo aperto con i nostri team, creando un ambiente collaborativo e positivo. Il miglioramento è percepito come una sfida motivante e non come un mero obiettivo” aggiunge Altariva. L’approccio di Crossnova ha favorito un cambio di mentalità tra i dipendenti, stimolando la partecipazione attiva e il coinvolgimento di tutti nel processo di miglioramento. Crossnova è riuscita a trasferire competenze specifiche, consentendo al personale di affrontare in autonomia progetti di miglioramento e sviluppare una mentalità orientata al Problem Solving.
Inoltre, Crossnova ha portato innovazione anche nei metodi di monitoraggio e valutazione dei risultati, implementando strumenti di analisi. Questi ultimi permettono a Valmet Tissue di misurare in modo continuo l’impatto dei cambiamenti introdotti. Questo approccio consente di avere una visione chiara dei progressi e di prendere decisioni più rapide e più agili.
Altariva evidenzia infine come la partnership con Crossnova sia stata fondamentale per stimolare un cambiamento culturale duraturo in azienda. Attraverso una collaborazione proattiva e orientata ai risultati, Crossnova ha saputo interpretare appieno la visione sul miglioramento continuo. Questo ha permesso di ottenere maggiore competitività, qualità del prodotto e soddisfazione dei clienti.
Conclusioni
L’esperienza descritta dimostra l’efficacia di un approccio strutturato basato su metodologie avanzate come il Lean Six Sigma. Con visione globale e forte attenzione alla formazione, l’azienda ha creato una cultura del miglioramento che si estende a tutti i livelli e settori. Il percorso di Continuous Improvement, oltre a garantire benefici operativi, rappresenta un investimento strategico. Si tratta senza dubbio di un investimento che contribuisce a rafforzare la competitività e a sostenere una crescita sostenibile nel lungo termine.
Se anche la tua azienda vuole ottenere risultati concreti e migliorare l’efficienza operativa, contattaci oggi stesso per scoprire come avviare un progetto di Miglioramento Continuo.